www.industria-online.com
23
'22
Written on Modified on
LIMITAZIONI DEI ROBOT INDUSTRIALI
Oggi, i robot industriali vengono utilizzati in quasi tutti i settori, dall'automotive alla plastica fino alla tecnologia medica. Offrono molti vantaggi agli stabilimenti di produzione e stanno spianando la strada alle fabbriche intelligenti del futuro. Tuttavia, nella scelta delle apparecchiature robotiche i produttori devono considerare alcuni limiti. In queste pagine Neil Ballinger, direttore EMEA presso il fornitore di parti per l'automazione EU Automation, analizza questi limiti e come superarli.
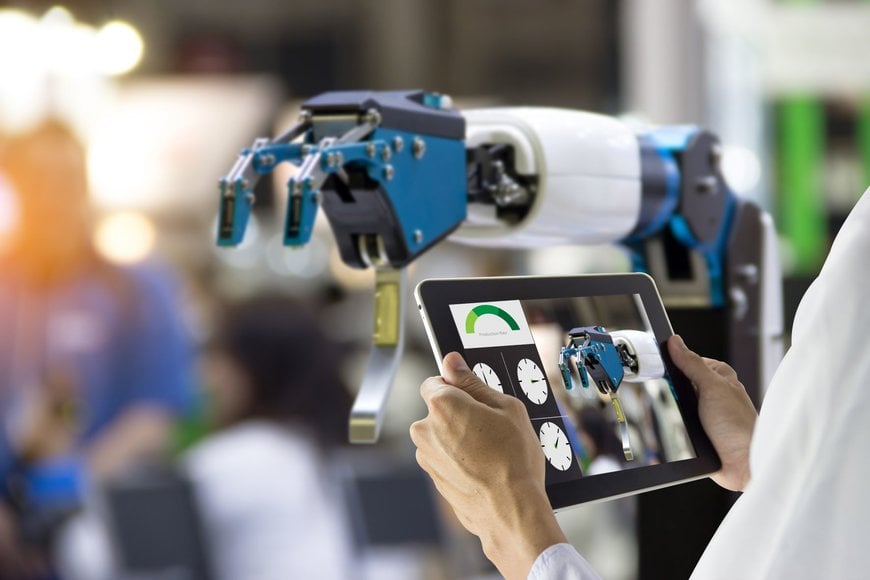
Secondo Fortune Business Insights, la necessità di automatizzare i processi è in aumento e si prevede che entro il 2028 il mercato dei robot industriali raggiungerà i 31,3 miliardi di dollari. I produttori diventano sempre più consapevoli dei potenziali vantaggi aziendali e produttivi derivanti dall'implementazione dei robot. Tuttavia, i robot industriali non sono privi di inconvenienti. Ecco alcuni dei loro limiti più comuni e qualche suggerimento su ciò che i produttori possono fare per superarli.
Convenienza
In generale, i robot industriali richiedono un ingente investimento iniziale, inclusi i costi aggiuntivi di installazione e configurazione. I produttori devono anche considerare i costi di manutenzione futuri e la necessità di componenti aggiuntivi.
Analogamente, la robotica è un settore in costante evoluzione, con un mercato che presenta continuamente macchine aggiornate. Investire regolarmente in nuovi robot potrebbe essere uno sforzo eccessivo per alcune aziende, in particolare per quelle più piccole che potrebbero fallire nel tentativo di stare al passo con le tendenze industriali.
Tuttavia, i robot industriali possono aiutare i produttori a tagliare i costi in diverse aree. Possono ridurre i costi di produzione e aumentare i profitti ottimizzando il lavoro. Una chiara strategia di investimento e un piano finanziario ben definito incrementano le probabilità di ottenere un rapido ritorno sull'investimento nei robot.
Un'altra alternativa intelligente è investire in robot ricondizionati. Normalmente, i robot usati costano la metà di quelli nuovi, pur mantenendo la loro efficienza e operabilità.
Sicurezza
I robot industriali sono sempre stati considerati in qualche modo pericolosi nell'officina di produzione. Ed esistono ragioni plausibili: si tratta di apparecchiature ingombranti e instabili in grado di muoversi a velocità molto elevate. Le macchine più vecchie sono anche prive delle capacità sensoriali per rilevare la vicinanza di esseri umani, il che le rende soggette a pericolose collisioni e incidenti. Per questo motivo, molti produttori aggiungono gabbie o divisori per separare i robot dai loro colleghi umani.
In tempi più recenti, con l'introduzione dei robot collaborativi, più piccoli, leggeri e progettati appositamente per il lavoro con gli umani, la sicurezza è diventata una delle principali priorità nell'automazione industriale. Sono aumentate le pratiche regolamentari attuate sia per i robot industriali pesanti che per i cobot.
Anche se c'è ancora molto da fare per raggiungere la sicurezza assoluta in fabbrica, i progressi in corso sono evidenti. Le nuove tecnologie come barriere luminose, scanner laser e dispositivi di rilevamento della presenza sono ampiamente accettate come metodo per aumentare la sicurezza umana.
Una buona prassi per i produttori è anche condurre una valutazione del rischio individuale della propria linea di produzione e formare i lavoratori sui modi in cui reagire a un potenziale incidente.
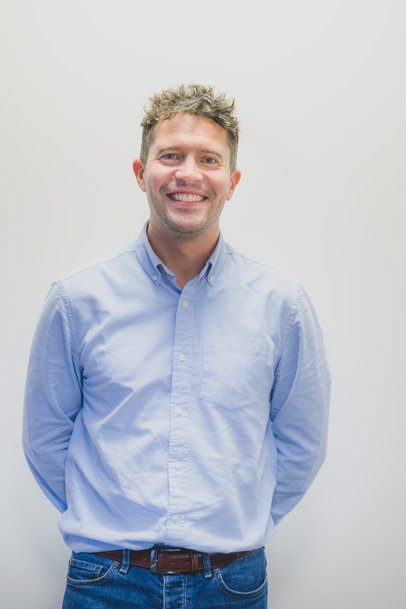
Difficili da istruire
Per eseguire i loro compiti, i robot industriali devono essere programmati e istruiti da esperti, quindi le aziende devono assumere ingegneri e programmatori competenti per supervisionarne l'installazione. Inoltre, quando vengono sviluppati nuovi software o lanciati nuovi robot sul mercato potrebbe essere necessaria una riqualificazione del personale esperto. La programmazione incorretta di un robot può portare a malfunzionamenti e lesioni al personale nelle sue vicinanze.
Tuttavia, negli ultimi anni è stato implementato un nuovo metodo di addestramento dei robot, la programmazione no-code o low-code. Consente ai dipendenti con poca esperienza di codifica di configurare un robot utilizzando la modellazione visiva e le interfacce utente drag-and-drop. Grazie al formato facile da usare delle piattaforme no-code e low-code, i robot possono essere riprogrammati facilmente per lavori diversi attraverso la regolazione del loro braccio. Mentre in precedenza un'azienda avrebbe avuto bisogno di più robot, oggi è sufficiente un semplice aggiustamento che può essere effettuato da una persona senza conoscenze tecniche specifiche, consentendo un risparmio di tempo, spazio e denaro.
Le piattaforme low-code e no-code presentano una tendenza in aumento, con l'84% delle imprese negli Stati Uniti, nel Regno Unito, in Canada e in Australia che implementano piattaforme di sviluppo low-code per ridurre le necessità di codifica.
I robot industriali hanno dimostrato la capacità di semplificare il lavoro umano, offrire un rapido ROI ai produttori e ottimizzare la produzione. Ciononostante, non sono privi di limitazioni. Sono più difficili da addestrare rispetto agli umani, richiedono elevati costi di investimento e manutenzione e pongono sfide per la sicurezza. Anche se si tratta di preoccupazioni legittime per i produttori, è possibile affrontarle e superarle con un'attenta pianificazione e nuove tecnologie. Noi di EU Automation riteniamo che i robot industriali siano risorse indispensabili per le fabbriche intelligenti e siamo sempre al passo con le ultime novità nei loro sviluppi.
www.euautomation.com
Richiedi maggiori informazioni…