www.industria-online.com
14
'20
Written on Modified on
EFFICIENZA ENERGETICA NELLE FABBRICHE INTELLIGENTI: UN MODO EFFICACE PER RIDURRE I COSTI OPERATIVI
Il concetto di fabbrica intelligente è in continua evoluzione da diversi anni, e si sta avvicinando sempre più all’obiettivo di garantire una comunicazione armoniosa tra tutte le apparecchiature presenti in produzione e i sistemi di gestione generale dell’azienda. In definitiva, l’intento è quello di garantire l’ottimizzazione della produttività e della qualità, dalle quotazioni e dagli ordini alla produzione e alla spedizione. Questa transizione costituisce anche un’opportunità ideale per affrontare un aspetto a volte trascurato del funzionamento intelligente degli impianti: l’efficienza energetica.
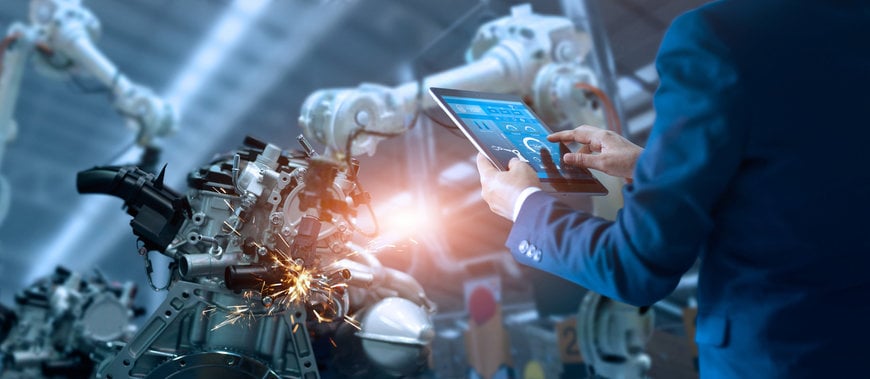
Negli ultimi anni sono state introdotte sul mercato molteplici soluzioni innovative e orientate al futuro, che offrono una misurazione intelligente e in tempo reale del consumo di elettricità, gas e acqua. Grazie alla conoscenza e allo sfruttamento di questi dati di misura, l’efficienza energetica può essere considerata un elemento essenziale dell’Industria 4.0.
Come dimostrano molti studi, le fabbriche sono tra i maggiori consumatori di energia al mondo. Tuttavia, l’elettricità è essenziale per la continuità e la qualità del processo di produzione lungo tutta la filiera. È quindi fondamentale garantire l’efficienza energetica in ogni momento.
La maggior parte delle fabbriche ospita al suo interno macchine, sistemi e apparecchiature che consumano energia: macchine utensili, linee di produzione, nastri trasportatori, motori, sistemi di riscaldamento, ventilazione e condizionamento, caldaie, generatori, illuminazione e così via. Con l’impiego delle tecnologie intelligenti appropriate, i responsabili degli impianti non devono più effettuare letture dei consumi energetici a intervalli predefiniti, come avviene con i sistemi di gestione dell’energia convenzionali. I sistemi convenzionali di gestione dell’energia forniscono un’istantanea del consumo di energia, ma non contribuiscono a ridurre il consumo di energia, identificare le tendenze per anticipare i picchi o fornire raccomandazioni per migliorare l’efficienza.
Al contrario, il monitoraggio intelligente consente analisi in tempo reale che aiutano a ottimizzare l’efficienza energetica. Inoltre, la misurazione intelligente consente di monitorare il consumo di energia non solo nel punto di distribuzione, ma anche in diversi punti di consumo all’interno dell’impianto.
La trasparenza dei flussi di energia e dei dati è essenziale per studiare il potenziale di ottimizzazione. Quando questi flussi sono anche integrati con i sistemi IoT nel cloud, è possibile ottenere e utilizzare informazioni preziose per ottimizzare l’intero impianto e attività produttive.
In definitiva, l’adozione di un ecosistema di soluzioni intelligenti che promuovono l’efficienza energetica nell’Industria 4.0 offre molti vantaggi in una varietà di settori, tra cui la gestione dell’energia, la connettività e il controllo remoto delle attività industriali. Soluzioni sostenibili come quelle presentate in questo articolo contribuiscono ad aumentare l’efficienza energetica e la produttività degli impianti industriali, garantendo al contempo che le fabbriche siano più sicure e più connesse.
PANORAMICA DI MERCATO
A Maisach, in Germania, il magazzino e centro di distribuzione del grossista di materiale elettrico Rexel esemplifica perfettamente questa tendenza, facendo leva sulle ultime soluzioni di monitoraggio energetico basate su cloud di Siemens per ridurre i suoi costi annuali di energia elettrica del 25-30%.
«I sistemi energetici e le fonti di energia rinnovabile sono sempre più distribuiti, e richiedono soluzioni moderne e intelligenti, basate sul monitoraggio dei consumi », spiega Ricardo Radowski, Business Development Manager presso Rexel Germania.
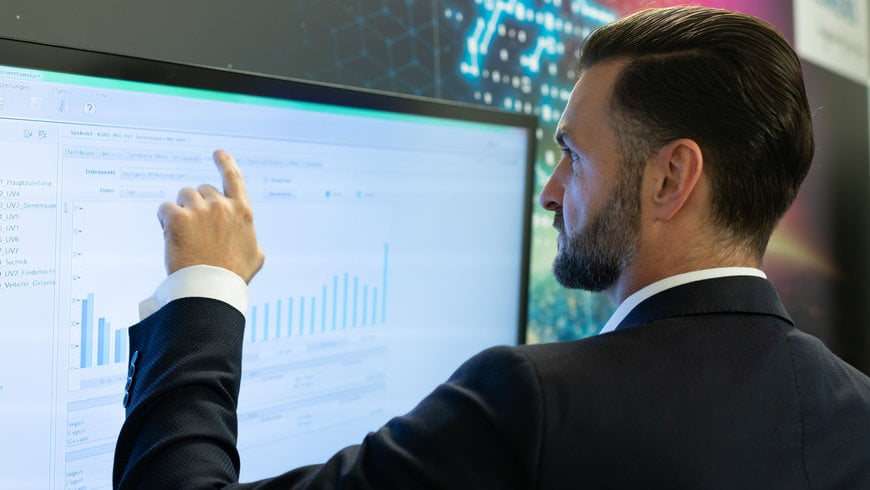
Nello stabilimento Rexel a Maisach, dati come la tensione, la corrente e la potenza delle linee elettriche - e di ogni fonte di consumo fino al livello macchina - vengono ora registrati in modo continuo.
Il sistema di monitoraggio elettrico di Siemens comprende software e dispositivi di misura della gamma Sentron. Sono state installate più di 100 unità della serie 7KM PAC. Oltre ai dati energetici, queste unità forniscono informazioni precise sullo stato della distribuzione dell’energia, letture accurate e una migliore gestione dei picchi di carico. I valori misurati consentono inoltre di valutare lo stato dei sistemi e la qualità della rete.
Attraverso l’interfaccia MindConnect Nano, i dati energetici raccolti nello stabilimento Rexel vengono trasferiti direttamente a MindSphere, il sistema operativo aperto cloud-based per l’Internet of Things di Siemens.
«Ora abbiamo visibilità sui flussi di energia », fa notare Ricardo Radowski. «Questo ci ha permesso di scoprire, in maniera sorprendente, che l’illuminazione rappresentava una parte importante dei nostri consumi. Quindi presto sostituiremo il nostro sistema di illuminazione con una soluzione più intelligente che consuma l’80% di elettricità in meno. »
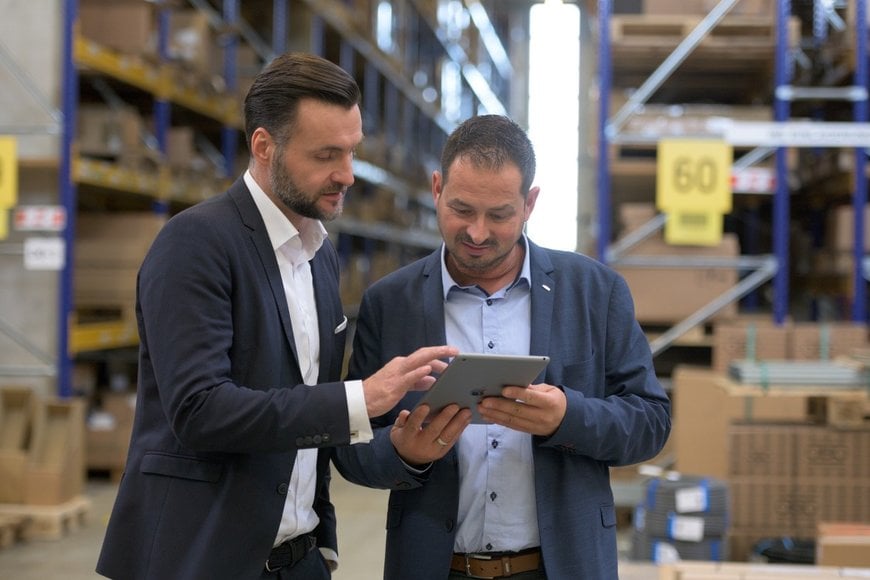
I risultati dell’analisi dei dati sono presentati in modo chiaro e accessibile su diversi dispositivi per la massima trasparenza in tempo reale.
Rexel ha installato la stessa soluzione nel suo centro di distribuzione a Weisskirchen, in Austria, valorizzando ulteriormente la connessione cloud.
«Abbiamo deciso di connetterci al cloud per sfruttare le opportunità associate al fatto che abbiamo diversi siti produttivi, e le numerose possibilità offerte», afferma Ricardo Radowski. «Ad esempio, ora possiamo facilmente confrontare l’efficienza energetica degli stabilimenti e condividere informazioni e best practice. »
MONITORAGGIO GLOBALE DELL’EFFICIENZA ENERGETICA
Situazione simile nella fabbrica intelligente di Salonit Anhovo in Slovenia. Grazie all’adozione di una soluzione basata su tecnologia LoRaWAN di Solvera Lynx, Salonit Anhovo si colloca oggi tra i primi 10 cementifici europei in termini di efficienza energetica.
Al fine di rispettare le normative europee e raggiungere gli obiettivi di riduzione del consumo di energia, Salonit Anhovo ha deciso di avviare un progetto di gestione energetica.
«La nostra azienda intendeva acquisire una conoscenza approfondita dei flussi di energia nell’impianto, e cercavamo un sistema in grado di elaborare automaticamente i dati relativi al consumo energetico », spiega Magda Gabrijelcic, Energy Manager di Salonit Anhovo.
Il progetto richiedeva una soluzione su misura per ottimizzare i processi di produzione ad alta intensità energetica: Salonit Anhovo consuma ogni anno oltre 90 GWh di elettricità, 8 GWh di gas e 400.000 m3 di acqua. Il costo totale del consumo energetico dell’azienda supera i 6 milioni di euro all’anno.
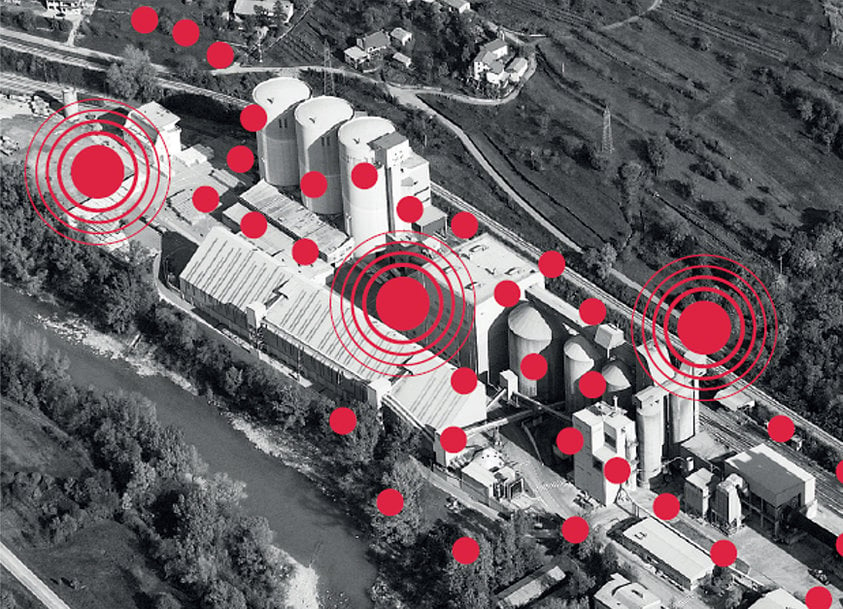
Il sito produttivo di Salonit Anhovo si estende su una superficie di oltre 6 km2.
Il progetto si è rivelato complesso a causa di un ambiente industriale gravoso caratterizzato da elevata umidità, temperature estreme e ampie aree di produzione.
«Le apparecchiature LoRaWAN di Solvera Lynx ci hanno aiutato a concentrarci sul potenziale di risparmio energetico del progetto, senza doverci preoccupare di aspetti hardware come il cablaggio », sottolinea Magda Gabrijelcic.
La trasmissione dei dati viene effettuata dal sistema di comunicazione ComBox.L, che ha un’elevata autonomia ed è ideale per gli ambienti industriali difficili. In totale sono stati installati 36 dispositivi certificati ComBox: 11 contatori per il gas, 10 per l’acqua, 5 per l’aria compressa e 10 elettrici. I dati vengono raccolti e analizzati dalla piattaforma software GemaLogic.
Una volta implementato il sistema di gestione dell’energia basato sul protocollo LoRaWAN, Salonit Anhovo ha rapidamente ottenuto risultati concreti e ha raggiunto gli obiettivi principali del progetto: la supervisione complessiva dell’efficienza e la riduzione dei consumi energetici.
«Dopo 16 mesi di utilizzo, siamo estremamente soddisfatti della nostra scelta », dichiara Magda Gabrijelcic. «Il sistema di gestione dell’energia composto da apparecchiature ComBox.L CI, tecnologia LoRaWAN e software GemaLogic si è rivelato perfetto per le nostre esigenze. »
RISULTATI CONCRETI NELLA RIDUZIONE DEL CONSUMO DI ENERGIA
Advantech ha sviluppato una soluzione hardware e software completa e integrata per trasformare rapidamente e facilmente gli impianti in siti intelligenti e più redditizi. L’azienda ha poi implementato questa soluzione nei suoi stabilimenti.
«Il nostro modello unico di co-creazione basato sulla partnership con i fornitori di SRP (Solution Ready Platforms) ci permette di offrire una soluzione completa [hardware e software] su misura per aderire immediatamente ai requisiti di Industria 4.0 », commenta Jash Bansidhar, Managing Director di Advantech. «Non è necessario dedicarsi alla organizzazione dei minimi dettagli per ciascun progetto. I vari componenti hardware e software sono già stati testati in loco e sono reciprocamente compatibili, il che garantisce un’implementazione molto rapida. »
L’azienda ha progettato e perfezionato questa soluzione innovativa per implementare l’Industria 4.0 nei propri impianti, aumentando significativamente la produttività e riducendo i costi di consumo energetico. Il ritorno dell’investimento è stato molto rapido.
In Europa, Advantech ha realizzato un centro di manutenzione a Eindhoven, nei Paesi Bassi, che rappresenta un eccellente esempio del potenziale dell’automazione industriale e dei sistemi sviluppati dall’azienda. La gestione del magazzino, il controllo in tempo reale e i sistemi di produzione sono monitorati tramite un cruscotto digitale che fornisce un controllo completo su tutti i dati strutturali per garantire un’analisi costante delle informazioni essenziali. Advantech può quindi dimostrare concretamente in prima persona a clienti e visitatori i risultati ottenuti in termini di produttività ed efficienza energetica.
Autore: Stefano CAZZANI
MIGLIOR GESTIONE DELL’ENERGIA GRAZIE ALL’INTELLIGENZA ARTIFICIALE
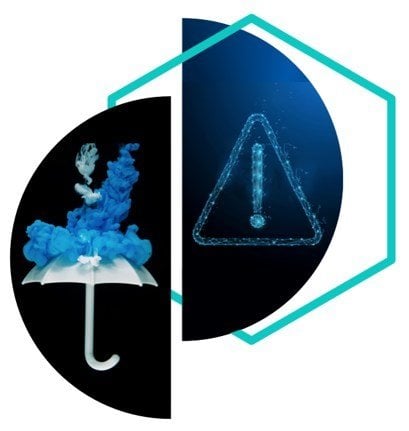
ABB e Verdigris Technologies hanno sviluppato degli algoritmi di apprendimento automatico per anticipare i picchi di consumo ed identificare le strategie di prevenzione. In particolare, ABB sfrutta l’intelligenza artificiale (AI) per aiutare le fabbriche e gli altri stabilimenti industriali a migliorare la gestione dell’energia e ad evitare gli aumenti dei tassi applicati ai picchi di consumo di energia elettrica.
L’azienda ha potenziato il sistema ABB Ability EDCS (Electrical Distribution Control System) con due applicazioni ottimizzate per l’AI: Energy Forecasting e Intelligent Alerts.
Energy Forecasting contribuisce a ridurre le bollette dell’energia elettrica riducendo i costi associati ai picchi di domanda. Intelligent Alerts utilizza algoritmi di autoapprendimento per aiutare i clienti a gestire meglio le loro risorse identificando i problemi prima che la situazione peggiori.
ABB Ability Energy Forecasting sfrutta le capacità dell’intelligenza artificiale per fornire ai responsabili degli impianti previsioni accurate sui consumi energetici. In breve, Energy Forecasting consente ai manager di prendere decisioni tempestive e di ridurre i picchi di consumo imprevisti riprogrammando o disattivando i carichi non critici, sfruttando così al meglio le tariffe delle fasce orarie.
L’intelligenza artificiale di Energy Forecasting si basa sulle reti neurali per identificare e assimilare le tendenze all’interno di un’area o legate al consumo energetico di un impianto, tenendo conto anche dei dati meteorologici. Utilizzando le previsioni del tempo e i dati storici, Energy Forecasting è in grado di prevedere il consumo di energia in kW per le prossime 24 ore, aggiornando i propri dati ogni 15 minuti.
ABB Ability Intelligent Alerts utilizza il machine learning per aiutare i clienti a gestire meglio le risorse strategiche. L’applicazione viene a conoscenza dei vari fattori di influenza dell’impianto e delle sue risorse chiave in modo da poter limitare le distorsioni causate da falsi allarmi e dal sovraccarico di informazioni. Ciò consente al personale delle utility di concentrarsi su compiti più produttivi. Intelligent Alerts identifica anche le aree principali e fornisce raccomandazioni per accelerare e migliorare le azioni correttive.
www.abb.com
SOLUZIONE DIGITALE PER LA GESTIONE DELL’ENERGIA NEGLI IMPIANTI
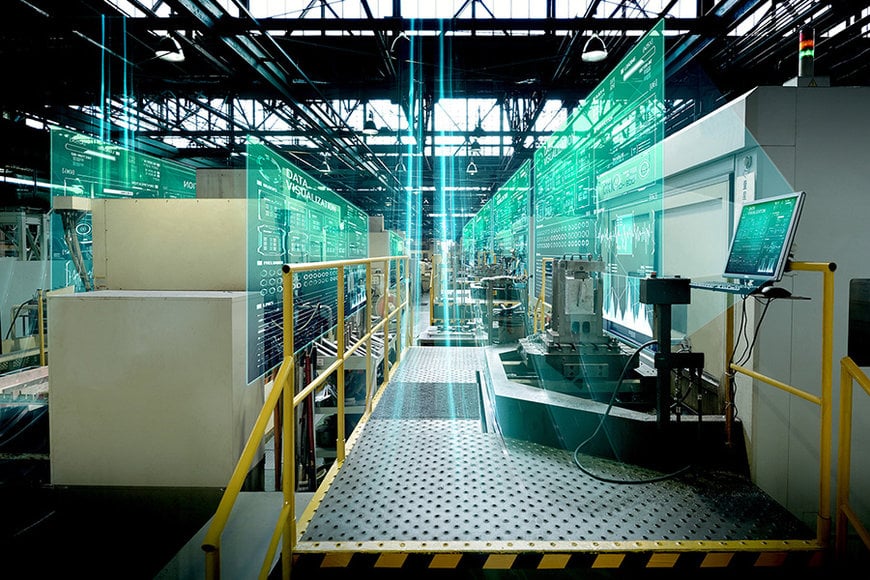
Mitsubishi Heavy Industries (MHI) ha lanciato ENERGY CLOUD Factory, un pacchetto di servizi che sfrutta le tecnologie AI e IoT. La soluzione si rivolge in particolare alle aziende che utilizzano Energy Cloud, il servizio di soluzioni energetiche di MHI.
Utilizzando i dati acquisiti da Netmation eFinder, il sistema sviluppato autonomamente da MHI per raccogliere dati sul funzionamento delle apparecchiature, il sistema consente il monitoraggio visivo dei tassi di utilizzo e del consumo energetico delle apparecchiature presenti in produzione. Inoltre, le prestazioni complessive di un impianto vengono valutate in base a parametri che consentono di stabilire il punteggio ENERGY CLOUD, un recente indicatore chiave di performance che integra indici per misurare la produttività e il consumo energetico di processo. L’esclusiva tecnologia AI fornisce anche previsioni sul rendimento futuro dell’impianto.
www.mhi.com
SISTEMA DI MONITORAGGIO DEL CARICO CON COMUNICAZIONE IO-LINK
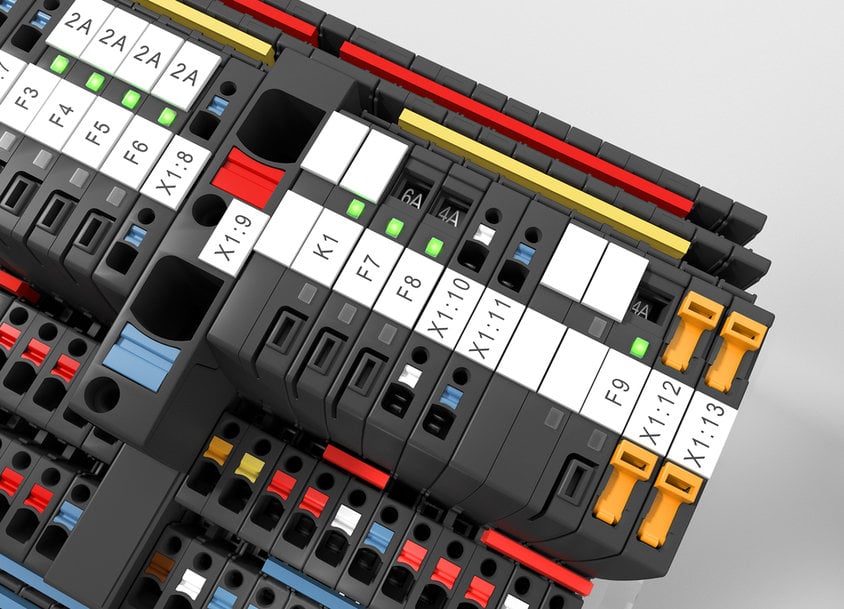
Weidmüller ha lanciato il sistema di monitoraggio del carico topGUARD con interfaccia di comunicazione IO-Link.
topGUARD fornisce agli utenti diverse opzioni per il controllo remoto delle attività produttive, registra i dati di funzionamento per un monitoraggio affidabile e ottimizzato dello stato, e offre la protezione delle tensioni di sistema a 24 V. Questo collegamento intelligente in rete di macchine, armadi elettrici e sistemi IT abilita soluzioni di controllo, monitoraggio e analisi completamente nuove.
IO-Link è considerata una delle tecnologie chiave per l’implementazione dei concetti dell’Industria 4.0 e dell’Internet of Things. Con il sistema di monitoraggio del carico topGUARD di Weidmüller, che protegge in modo intelligente i carichi DC e comunica tramite IO-Link, gli utenti possono implementare una comunicazione continuativa dalla fabbrica al cloud.
È sufficiente collegare il modulo IO-Link e integrare un file IODD per la parametrizzazione e il controllo, fornendo così all’utente tutti i dati di funzionamento necessari.
www.weidmueller.com
Richiedi maggiori informazioni…