www.industria-online.com
05
'20
Written on Modified on
Il rivoluzionario potenziale della manifattura additiva
La crescente popolarità della stampa 3D e delle tecnologie additive è di buon auspicio per il futuro sostenibile del pianeta Terra.
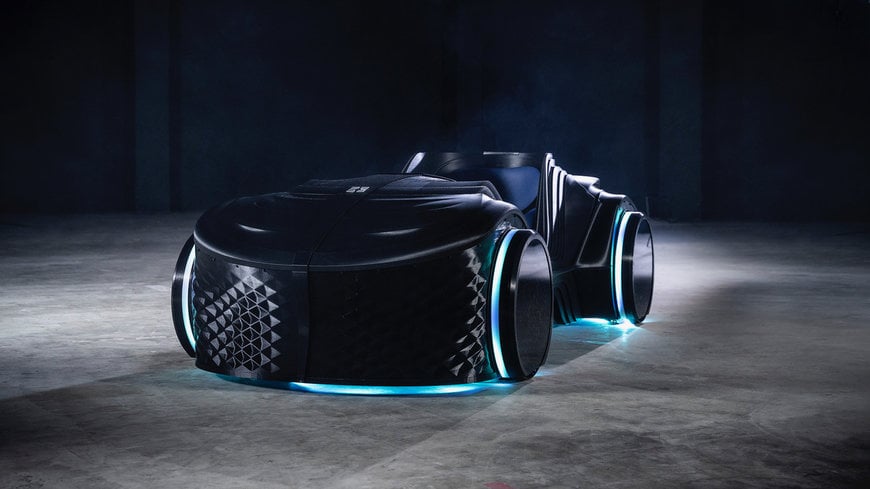
La stampa 3D o produzione additiva (additive manufacturing) è stata descritta come una delle tecnologie più rivoluzionarie e dirompenti dell'era attuale - la chiave per il futuro dell’industria manifatturiera. Inventata all'inizio degli anni '80, è cresciuta enormemente in popolarità negli ultimi anni grazie alla rapida evoluzione e convergenza di diverse tecnologie dell'era digitale, rendendola facilmente accessibile sia ai professionisti che agli hobbisti. L’Additive Manufacturing (AM) o 3D Printing, un tempo appannaggio esclusivo di chi si occupava di prototipazione rapida, è oggi vista come la risposta per fabbricare interi prodotti o parti più o meno complesse, ovunque e in qualsiasi momento. A differenza della tecnologia di produzione convenzionale o sottrattiva, che si avvale di processi come la fresatura, il taglio o la rettifica per rimuovere il materiale in eccesso, la produzione additiva è basata sull'aggiunta di materiale, strato per strato, per formare un oggetto completo o una sua parte, utilizzando per la progettazione un software CAD o uno scanner 3D. Le tecnologie additive prevedono l’utilizzo di svariati processi e materiali diversi. Ad esempio, i materiali utilizzati vanno dai termoplastici ai metalli, dalle ceramiche ai biochimici, questi ultimi spesso utilizzati per realizzare impianti per applicazioni medicali.
Uno dei principali vantaggi della produzione additiva è che facilita la produzione di pezzi personalizzati su richiesta a costi relativamente accessibili - i pezzi stampabili vanno dalla ruota perduta di un'automobilina giocattolo alle ruote cingolate del Mars Rover. Ancora più importante, il processo additivo consente di progettare e realizzare pezzi con geometrie complesse che riducono il peso, e che al tempo stesso sono più resistenti, nonché parti difficili e/o costose da produrre con i metodi tradizionali. L'esempio dell'ugello del carburante progettato e stampato in 3D da GE per il motore a getto LEAP è ben noto. Precedentemente assemblato a partire da 20 componenti separati, questo ugello complesso, grande come una noce, è ora una meraviglia dell’ingegneria ed è realizzato in un unico pezzo, grazie alla stampa 3D. Inoltre, pesa il 25% in meno rispetto alla sua controparte prodotta con i metodi tradizionali, è cinque volte più resistente e il 30% più economico da produrre. Come sostiene Janne Kyttanen, un visionario della stampa 3D e inventore della tecnologia 3DTI - la prima tecnologia di produzione in assoluto che integra la stampa 3D con la personalizzazione di massa - l'unico limite nelle applicazioni dell’additive manufacturing è la creatività, o la sua mancanza.
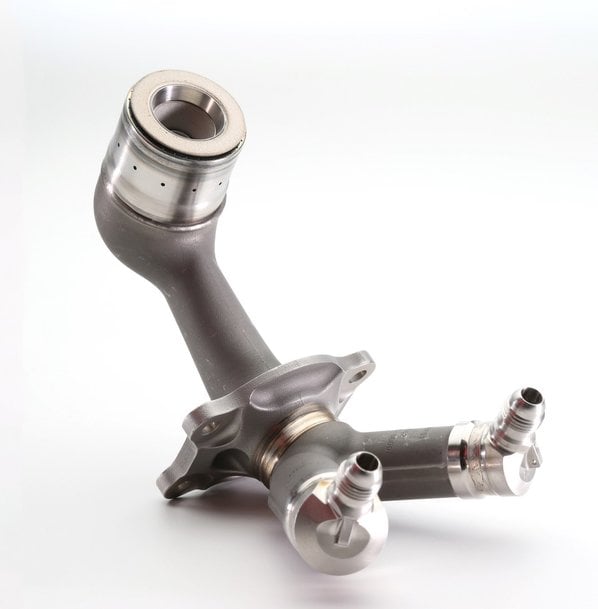
L'ugello del carburante prodotto da GE per il motore a getto LEAP
I vantaggi sono molteplici, ma il processo additivo non è privo di svantaggi, primo fra tutti l'elevato costo, sia in termini di investimenti iniziali che di spese operative. Quest'ultimo è dovuto all'elevato costo dei materiali, che nella maggior parte dei casi sono forniti dai produttori di hardware, e vincolati ad accordi OEM. La struttura dei costi delle tecnologie additive esclude generalmente anche la produzione di massa, soprattutto di pezzi di grandi dimensioni, in quanto l'economia in questo caso è chiaramente a favore dei processi di produzione convenzionali. Tuttavia, per esigenze particolari, le tecnologie additive offrono grandi vantaggi, indipendentemente dalle dimensioni e dai volumi di produzione. L'esempio di una staffa per sedili - una parte standard del settore automobilistico usata per fissare le cinture di sicurezza ai sedili e i sedili ai piani - prodotta presso General Motors utilizzando il software di progettazione generativa Autodesk, lo testimonia in modo evidente. Quello che era un pezzo scatolato composto da otto pezzi saldati insieme, ora è un ancoraggio dall'aspetto elegante, stampato in 3D in acciaio inossidabile. Il sostituto non è solo il 40% più leggero, ma anche il 20% più resistente e meno costoso da produrre, poiché riduce il numero di fornitori e il lavoro di saldatura. Non c'è da stupirsi, quindi, che ogni produttore di automobili oggi abbia investito in impianti per la produzione additiva, allo scopo di ottimizzare la progettazione dei veicoli per risparmiare sui costi. Un'auto media è composta da circa 30.000 pezzi. Sebbene non tutti i componenti possano essere prodotti con la stampa 3D, ce ne sono diversi che si possono rivelare molto adatti, come la staffa del sedile nell'esempio sopra citato, e che potranno sicuramente beneficiare dell’evoluzione tecnologica.
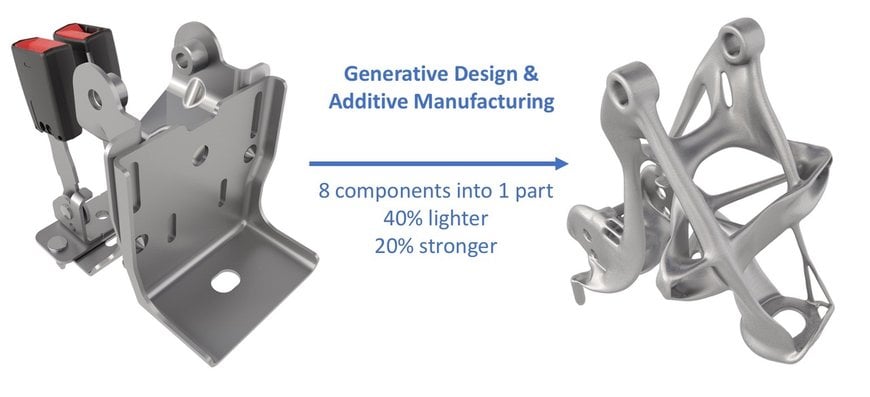
Il supporto del sedile prodotto da General Motor
Innovazioni a Formnext
A Formnext 2019 (Francoforte, novembre 2019), la più grande fiera europea dedicata alla produzione additiva e alle soluzioni di produzione intelligente di nuova generazione, aziende leader del settore come 3D Systems, Addup, BigRep, DMG Mori, EOS, Formlabs, GE Additive, HP, Markforged, Renishaw, Siemens, Stratasys, Voxeljet e molte altre hanno presentato diverse nuove e più efficienti tecnologie di produzione e soluzioni avanzate per l'utilizzo industriale - software, hardware, materiali e servizi - oltre a una pletora di annunci di legami e alleanze tecnologiche.
GE Additive, società del gruppo General Electric e leader mondiale nonché pioniere nelle tecnologie additive, ha presentato una serie di nuovi prodotti, tra cui l'Arcam EBM Spectra L, una stampante 3D a metallo che soddisfa la crescente domanda di mercato, soprattutto da parte dell'industria aerospaziale. Questo nuovo modello offre un volume di stampa più grande e una velocità più elevata, insieme ad un'architettura di sistema integrata, all'analisi della salute delle macchine e alle funzioni di automazione. La stampante Spectra L è stata sviluppata per aumentare la produttività e ridurre i costi per pezzo del 10%, grazie a un volume di stampa quasi doppio rispetto all'Arcam EBM Spectra H. La potenza del fascio di 4,5 kW aumenta la velocità di produzione del 20% rispetto all'Arcam EBM Q20plus. L'azienda ha inoltre lanciato la stampante a metallo Concept Laser M2 Serie 5, che soddisfa le elevate aspettative di qualità e ripetibilità dei pezzi da parte dei clienti, soprattutto nei settori aerospaziale e medicale altamente regolamentati e che, insieme all'industria automobilistica, sono tra i principali utilizzatori delle tecnologie additive.
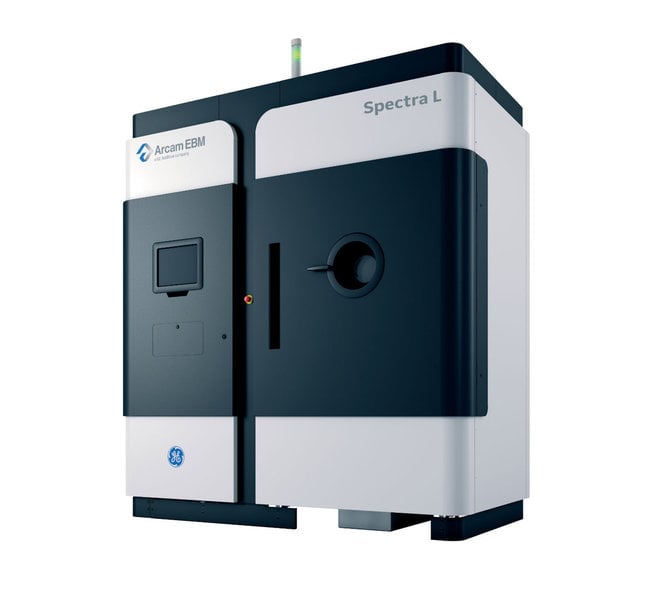
L'Arcam EBM Spectra di GE Additive
BigRep, l'azienda che sviluppa le stampanti 3D per la produzione in serie più grandi del mondo, ha presentato un concept di auto podcar elettrica a guida autonoma completamente stampata in 3D, la LOCI. Il prototipo LOCI è stato appositamente progettato come "soluzione di trasporto per l'ultimo miglio" in ambiente urbano, per l'utilizzo in aeroporti e stazioni ferroviarie, per i pendolari che si recano quotidianamente al lavoro e per il trasporto all’interno dei campus o per le consegne a domicilio. Sviluppato utilizzando la modellazione parametrica, LOCI sfrutta tutto il potenziale della produzione additiva e la sua flessibilità senza limiti. Il design del veicolo può essere facilmente personalizzato in base alle esigenze specifiche di un determinato luogo o di un’applicazione, adattando i materiali di costruzione, le proprietà strutturali e gli pneumatici speciali per i diversi terreni, il marchio commerciale e il sistema di generazione integrato a energia solare. A Formnext, l'azienda ha presentato tre diverse iterazioni di LOCI: Il modello LOCI Berlino è stata presentato come soluzione pendolare per campus con trasporto di una sola persona; il modello LOCI San Francisco come veicolo stretto adatto al pendolarismo urbano, mentre il modello LOCI Dubai è stato pensato per il trasporto aeroportuale, trasmettendo una sensazione di lusso di alto livello, con pannelli solari, spazio per i bagagli e pneumatici robusti adatti al clima del deserto.
Un altro importante lancio di BigRep avvenuto Formnext è stato il NEXT AGV, un veicolo a guida autonoma sviluppato in collaborazione con Bosch Rexroth, per l'utilizzo all’interno delle fabbriche intelligenti. Pensato per la produzione agile e intelligente, il veicolo NEXT AGV è stato stampato in 3D ed è alimentato per via induttiva tramite una rete elettrica e può fungere da vettore logistico automatizzato con una capacità di carico fino a 250 kg. Sulla piattaforma possono essere montati utensili e dispositivi aggiuntivi come i robot. Speciali ruote stampate in 3D con due diversi materiali consentono alla piattaforma di eseguire movimenti laterali.
3D Systems, l'azienda fondata nel 1983 da Chuck Hull, l'inventore della stampa 3D, ha presentato a Formnext 2019 quattro soluzioni di produzione progettate specificamente per i settori medicale, aerospaziale e automobilistico. L'azienda è in una posizione unica per offrire soluzioni specifiche personalizzate in base alle esigenze dei clienti con hardware, software, materiali e servizi professionali, integrando la manifattura additiva con negli ambienti di produzione tradizionali. Grazie a una partnership strategica con GF Machining Solutions, 3D Systems combina le sue soluzioni innovative e la sua esperienza nella produzione additiva con la leadership di GF Machining Solutions nella lavorazione di precisione. Ciò consente ai produttori industriali di combinare efficacemente le tecnologie additive e sottrattive per realizzare in modo più efficiente parti metalliche complesse con tolleranze ristrette e ridurre i costi operativi totali. Una delle soluzioni dimostrate presso lo stand congiunto è stato il processo di produzione per creare una staffa aerospaziale in sette fasi, che integra tecnologie additive, tecnologie di asportazione tradizionali e soluzioni software innovative per ottenere parti di alta qualità e ripetibili ad un costo per pezzo ottimizzato.
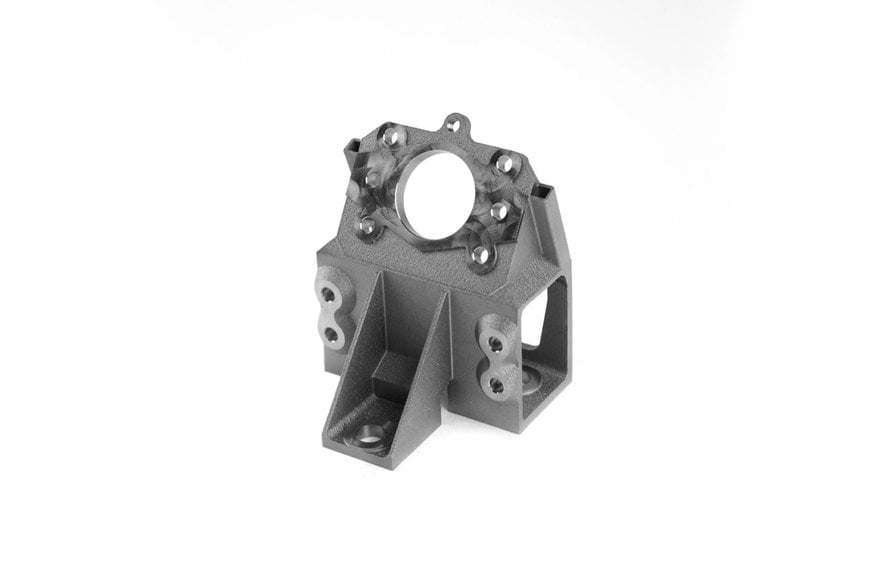
La staffa ibrida per applicazioni aerospaziali sviluppata da 3D Systems
EOS, fornitore leader mondiale di tecnologia nel campo della stampa industriale 3D di metalli e polimeri, ha presentato per la prima volta la sua tecnologia Fine Detail Resolution (FDR) per la lavorazione dei polimeri. EOS è il primo produttore a sviluppare una soluzione per la stampa 3D industriale a base di polveri con l'utilizzo di un laser a CO. Ciò rende possibile la produzione di pezzi estremamente delicati ma robusti, con superfici stampate ad alta risoluzione con fini dettagli e spessori delle pareti anche di soli 0,22 mm. Queste innovazioni aprono la strada a nuove applicazioni per la produzione in serie e offriranno un’ancora più ampia possibilità di scelta tra le soluzioni EOS per la stampa 3D dei polimeri. La tecnologia FDR combina il meglio di due mondi: la risoluzione dettagliata della stereolitografia (SLA) con la durata e la qualità della sinterizzazione laser selettiva (SLS). Presentata per la prima volta a Formnext, apre nuove possibilità per affrontare applicazioni completamente nuove nel campo della produzione additiva di pezzi polimerici, come ad esempio unità di filtraggio e canali dei fluidi, spine e altri componenti elettronici, nonché per beni di consumo come gli occhiali.
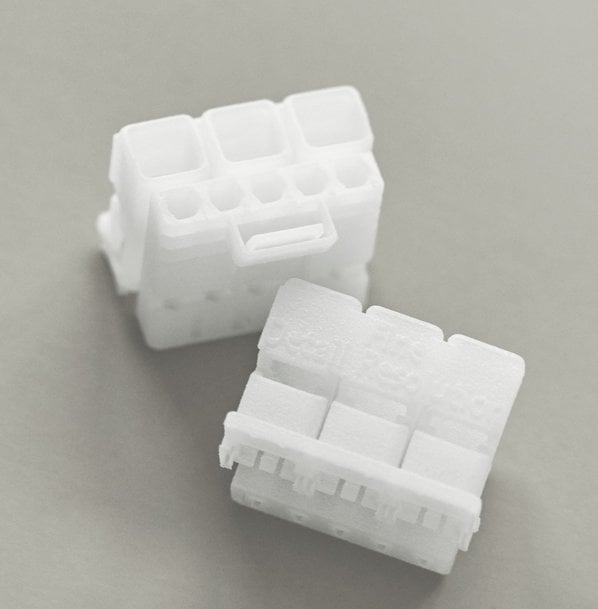
Spine stampate in 3D con la tecnologia FDR di EOS
Essentium ha annunciato l'espansione della sua piattaforma per la produzione additiva con l'introduzione di materiali ad alta temperatura (HT) e nuovi modelli della sua rinomata soluzione di stampa ad alta velocità Essentium High Speed Extrusion (HSE). La temperatura dell'ugello del nuovo modello HSE 180-S HT raggiunge i 550°C e utilizza un'ampia varietà di materiali per produrre pezzi in grado di resistere a temperature di 180°C. Introducendo sul mercato la tecnologia delle produzione additiva ad alta temperatura senza compromettere la velocità, la forza, la scala o l'economia, Essentium ha accelerato il potenziale di queste soluzioni su scala industriale e ha mantenuto il suo impegno di creare un ecosistema globale e aperto che mette i clienti in grado di controllare la loro innovazione. L'azienda ha anche introdotto quattro nuovi materiali, tra cui PEEK, Nylon ad alta temperatura (HTN), HTN-CF25 e HTN-Z (ESD safe), progettati per fornire un'elevata resistenza al calore, chimica e alla fatica e un'elevata resistenza per applicazioni industriali. Oltre ad introdurre la piattaforma di stampa 3D HSE ad alta temperatura, Essentium ha annunciato che integrerà il software Materialise 3D printing Magics Essentials con la stampante 3D Essentium HSE. L'integrazione tra il software e la stampante offre una suite FFF aperta e completa che supporta un flusso di lavoro end-to-end con tutte le caratteristiche necessarie per la produzione 3D su scala industriale in grado di trasformare le linee produttive delle aziende manifatturiere.
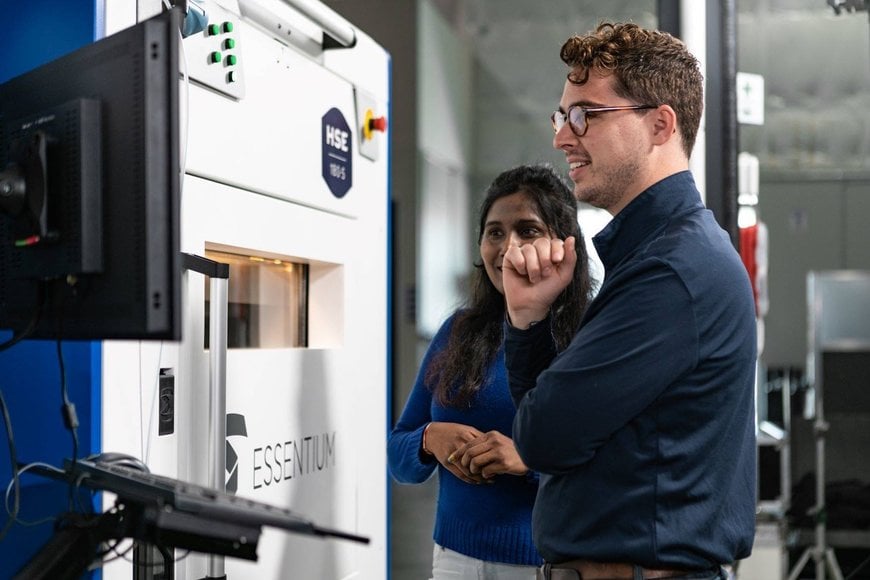
La nuova stampante HSE 180-S HT di Essentium
Un altro importante protagonista del settore, Renishaw, ha lanciato il software di monitoraggio acustico InfiniAM Sonic per completare la sua suite InfiniAM di strumenti di monitoraggio per la manifattura additiva. InfiniAM Sonic consente di rilevare gli eventi acustici all'interno della camera di stampa e di trasformare questi dati in informazioni utili sulla qualità della costruzione. Il software è il primo del suo genere nel settore della produzione additiva. Il pacchetto InfiniAM Sonic è installato nel sistema RenAM 500Q come opzione installabile in fabbrica e comprende quattro sensori di energia acustica per rilevare le vibrazioni all'interno della costruzione. Il sistema RenAM 500Q è dotato di quattro laser ad alta potenza da 500 W per raggiungere velocità di costruzione fino a quattro volte più veloci dei sistemi a laser singoli convenzionali. La massima efficienza viene raggiunta con il modello RenAM 500Q, in quanto i laser possono lavorare su tutta la piastra di costruzione, permettendo di gestire efficacemente l'interazione laser per garantire che la qualità non sia influenzata dall'interazione multi-laser durante l'elaborazione. Renishaw sta inoltre collaborando con Sandvik Additive Manufacturing per qualificare i nuovi materiali adatti per le applicazioni di produzione additiva. Tra essi vi sono un'ampia gamma di polveri metalliche, incluse nuove composizioni di leghe ottimizzate per il processo di fusione a letto di polvere laser (LPBF) e che forniscono proprietà superiori del materiale.
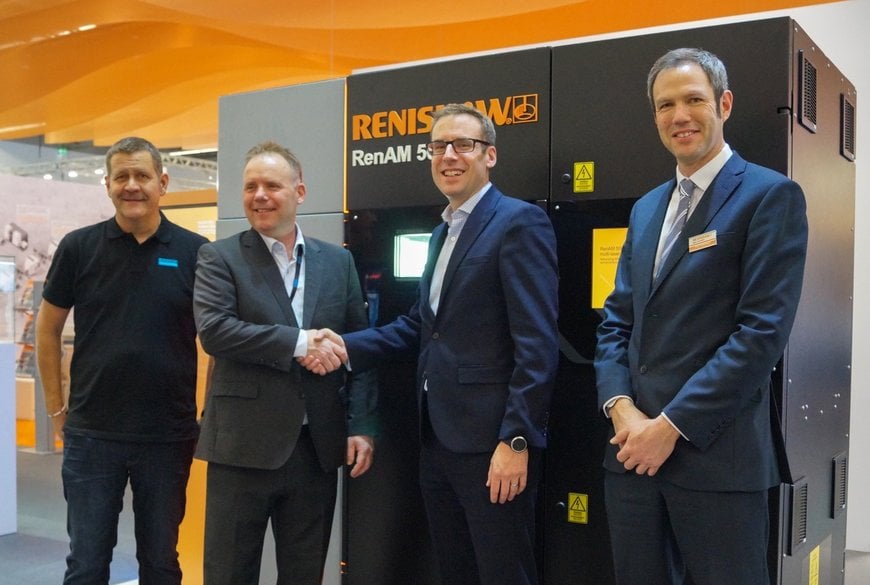
Il team Renishaw a Formnext 2019
Se la stampa 3D può replicare un oggetto semplicemente scansionando e stampando, si crea anche un problema di sicurezza. Una chiave può essere facilmente fotografata o scannerizzata e un duplicato può essere stampato ovunque. In occasione della fiera si è tenuta la premiazione di una tecnologia chiave per il futuro dell’industria e il premio è andato proprio a una chiave - non una chiave qualunque, ma la 'Stealth Key' stampata in 3D, progettata e prodotta da UrbanAlps AG, un produttore svizzero - vincitore del primo premio della sfida Purmundus a Formnext 2019. Utilizzando la tecnologia stealth, UrbanAlps ha creato un sistema di chiavi e cilindri fisici in cui il codice è ben nascosto sotto robuste e strette proiezioni. Poiché la chiave puramente meccanica non può essere scansionata, offre la massima sicurezza e funziona indipendentemente dai sistemi digitali - neutralizzando la minaccia, utilizzando efficacemente la stessa tecnologia.
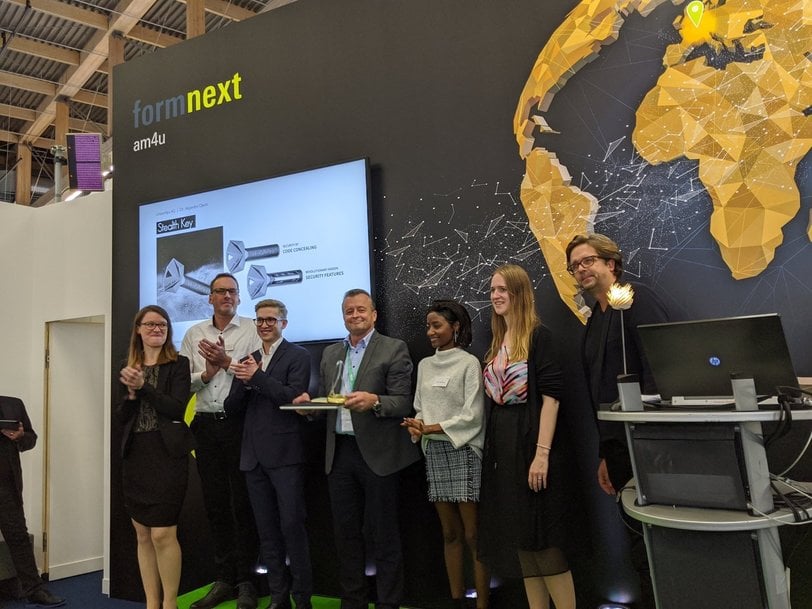
La Stealth Key si è aggiudicata il primo premio della sfida Purmundus
Questi sono solo alcuni esempi tra le soluzioni proposte dagli 852 espositori (erano 632 nel 2018) che hanno partecipato a Formnext 2019 e che rappresentano l'intera catena del valore aggiunto legata alle tecnologie additive. L'evento ha attirato oltre 34.000 visitatori provenienti da 99 paesi, a testimonianza della crescita a livello globale della produzione additiva.
La via da seguire
Le crescenti preoccupazioni per l’impatto ambientale e il cambiamento climatico hanno finalmente attirato l'attenzione dei governi e dei responsabili politici, così come delle industrie di tutto il mondo. La sostenibilità è il nuovo mantra, la neutralità del carbonio il nuovo obiettivo, dato che più di 60 paesi mirano a ridurre le emissioni di carbonio a zero entro il 2050, secondo quando indicato dalle Nazioni Unite. A metà del 2019, Bosch - fornitore globale di tecnologia e servizi - ha dichiarato che l'azienda diventerà neutrale dal punto di vista delle emissioni di carbonio nel 2020. Molte aziende stanno attuando i propri programmi per raggiungere lo stesso obiettivo.
Mentre il mondo si muove verso la sostenibilità, la stampa 3D avrà un ruolo importante da svolgere, soprattutto in tutti gli ambiti della mobilità. La leggerezza - ridurre il peso di tutte le forme di trasporto terrestre, aereo e marittimo - è la priorità assoluta per i costruttori di veicoli. Il software di progettazione generativa è la tecnologia abilitante che lo rende possibile. Quando General Motors ha riprogettato la staffa del sedile utilizzando la tecnologia di progettazione generativa di Autodesk con Fusion 360, il software ha proposto oltre 150 progetti alternativi, tra i quali è stato scelto il progetto considerato ottimale. Autodesk e BMW stanno lavorando all'utilizzo delle tecnologie di progettazione generativa e dei metodi di produzione additiva per creare un nuovo tipo di veicolo che possa essere più leggero, più veloce, più economico, più affidabile e più facile da produrre.
La combinazione di progettazione generativa e produzione additiva ha ampie applicazioni che vanno oltre la mobilità. La tecnologia ha un grande potenziale in molti altri campi in cui vengono utilizzati materiali - architettura e costruzioni, edifici e impianti, macchinari industriali e beni di consumo – e permette di ottenere incrementi di produttività e risparmi energetici, contribuendo a ridurre l'impronta di carbonio. A proposito di materiali, la stampa 3D ha anche fatto rapidi passi avanti nel settore alimentare, in particolare nel segmento dolciario, consentendo di realizzare design complessi e attraenti per torte e cioccolatini.
Grazie alla rapida evoluzione e alla continua riduzione dei costi, man mano che l'hardware e i materiali di consumo diventano più economici, la stampa 3D e la produzione additiva diventeranno sempre più popolari negli anni a venire. Dalle più semplici calzature alle potenti astronavi, la tecnologia sta rapidamente rivoluzionando il modo in cui questi prodotti vengono progettati e fabbricati, offrendo la chiave per promuovere un futuro sostenibile.
Autore: Bruno FORGUE
Richiedi maggiori informazioni…