KOHLER presenta K-HEM
K-HEM, l’unità ibrida di generazione di potenza combinata elettrica e meccanica.
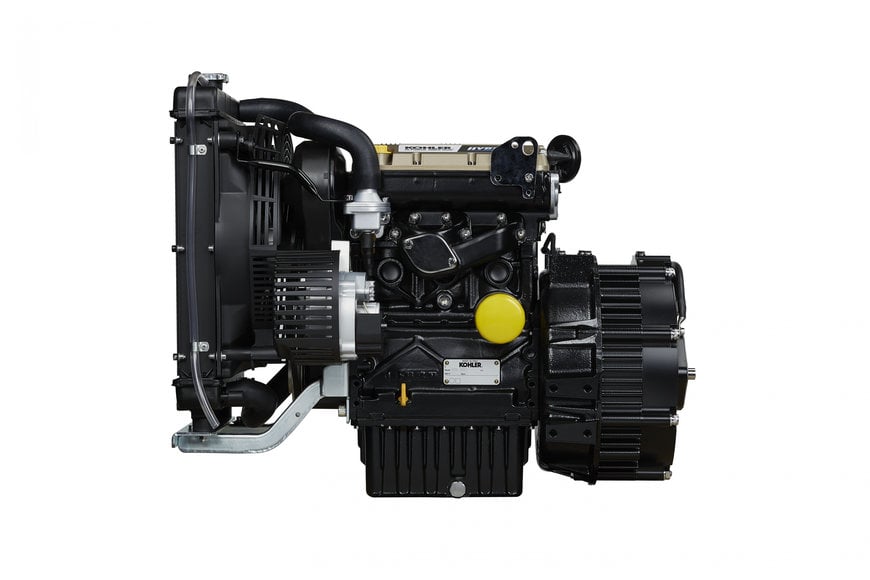
Alla luce dei cambiamenti che la nuova direttiva in materia di emissioni ha apportato al settore delle applicazioni off-road a partire dal 1° gennaio 2019, l’offerta di Kohler si è dotata di una famiglia di prodotti in grado di intercettare i nuovi bisogni dei costruttori del settore. Sul mercato esistono fonti di energia differenti e la scelta di Kohler non è quella di investigarne l’utilizzo e le peculiarità per metterle in competizione, ma quella di integrarle e farle convivere per riuscire a estrarne tutto il potenziale valore.
Nasce così K-HEM 1003, l’unità di generazione di potenza data dalla combinazione del motore diesel KDW 1003 da 18 kW conforme alla normativa Stage V e senza DPF, e del motore elettrico 48 Volt che garantisce 15 kW di picco e 9 kW continuativi. Dunque, l’unità è in grado di offrire più di 30 kW senza bisogno di utilizzare sistemi di post-trattamento dei gas di scarico; K-HEM può inoltre funzionare come generatore per sistemi di accumulo dell’energia.
Le caratteristiche dell’unità ibrida K-HEM sono studiate per tutta quella serie di applicazioni contraddistinte da cicli di lavoro discontinui che richiedono picchi di potenza (saldatori, rasaerba, trattori con accessori per l’agricoltura, ecc.) e di macchine che operano prevalentemente con cicli di lavoro costanti a bassi carichi che impediscono il raggiungimento delle temperature necessarie per lo svolgimento della rigenerazione passiva all’interno del filtro antiparticolato (piattaforme aeree, carrelli elevatori, ecc.).
Con K-HEM, la base di potenza è fornita dal motore termico, mentre i picchi di potenza sono garantiti dal motore elettrico; tale sistema, nel rispetto dei limiti indicati dalla normativa Stage V, permette alle macchine di evitare un’operazione di detaratura e garantisce elevati livelli di produttività: la centralina master integrata permetterà all’utilizzatore di monitorare e gestire le modalità di lavoro e le transizioni in base alle proprie esigenze.
Tutto ciò risulterà in macchine più leggere, compatte e performanti rispetto al passato, capaci di sfruttare tutti i vantaggi dell’integrazione della potenza meccanica e della potenza elettrica: riduzione della complessità del motore, assenza di sistemi di post-trattamento, immagazzinamento e sfruttamento dell’energia prodotta in eccesso grazie all’alternatore integrato, recupero dell’energia durante le fasi di frenata e di scarico, possibilità di gestire le operazioni grazie alla centralina master, riduzione delle emissioni gassose, della rumorosità e dei consumi, miglioramento delle performance e della modulazione della potenza grazie alla gestione integrata di ciascuna operazione.
- Più efficienza. Il motore diesel garantisce il massimo del rendimento in specifiche condizioni di esercizio, quindi l’unità ibrida permetterà di raggiungere più velocemente e più frequentemente i punti ottimali di lavoro, aumentando così l’efficienza del lavoro svolto e, di conseguenza, la produttività dell’applicazione.
- Operazioni di recupero. Grazie alla doppia funzione della componente elettrica che lavora come generatore o come motore ausiliare, sarà possibile recuperare energia dal sistema di trasmissione durante le fasi di frenata e di scarico della macchina e dallo stesso motore termico durante le fasi di lavoro a bassa richiesta di potenza. In questo modo, l’energia immagazzinata nelle batterie sarà disponibile quando la macchina richiederà di superare la soglia dei 18 kW termici installati, superando addirittura i 30 kW; ne risulta un notevole risparmio in termini emissioni, consumi e potenza termica installata.
- Integrazione perfetta. I costruttori di applicazioni non devono preoccuparsi per eventuali problemi di installazione dato che l’integrazione dell’unità ibrida con il sistema idraulico o la trasmissione meccanica è uguale a quella del motore diesel.
- Gestione puntuale. L’elevato livello di integrazione tra parte meccanica e parte idraulica reso possibile dall’unità ibrida permette una totale ottimizzazione della gestione della macchina: ciascun attuatore può essere gestito dal sistema idraulico o elettrico a seconda delle specifiche esigenze e controllato dalla centralina master che sovrintende il sistema. L’esempio più lampante è rappresentato dagli accessori agricoli: la possibilità di sganciarli dal sistema meccanico e di gestirli con il sistema elettrico, permette ora un elevatissimo livello di ottimizzazione delle operazioni.
Richiedi maggiori informazioni…