www.industria-online.com
12
'10
Written on Modified on
Giacitura di fibra ad alta velocità su grandi strutture complesse
Per dare impulso all’efficienza del carburante, è essenziale ridurre il peso degli aeromobili. Ciò non solo è molto importante in termini di costo, ma è essenziale per una avere una maggiore capacità, considerate le distanze sempre crescenti che si prevede verranno percorse dagli aeroplani del futuro. L’elevato rapporto robustezza-peso della fibra di carbonio è oggi una delle principali innovazioni, ma la necessità di alte velocità di produzione richiede macchine estremamente complesse. Electroimpact ha sviluppato una soluzione eccezionale che offre una velocità di giacitura automatizzata della fibra pari a 2000 pollici al minuto (50 metri al minuto). Ciò implica un sofisticatissimo sistema di controllo e sistemi di azionamento degli assi molto stabili e precisi. Andantex USA ha fornito tutti i componenti meccanici critici per azionare gli assi.
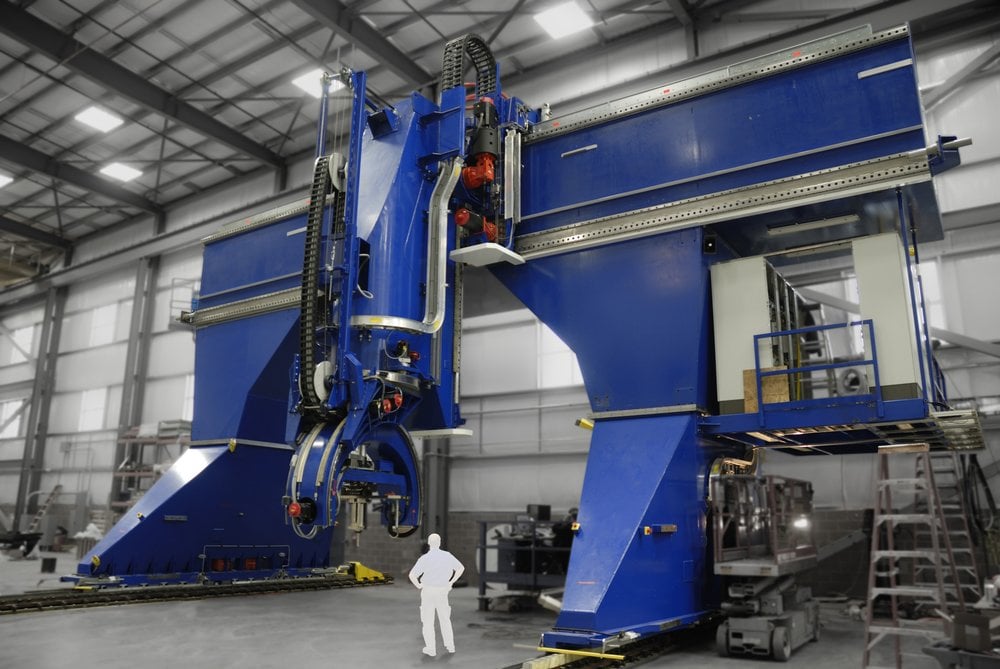
Electroimpact è un’azienda guidata da giovani ingegneri la cui missione è essere il principale fornitore di apparecchiature automatizzate per l’industria aeronautica mondiale. Electroimpact ha sviluppato la tecnologia Automated Fiber Placement (AFP), che permette di tagliare e aggiungere strisce di fibra di carbonio (tow) entro le tolleranze di giacitura stabilite dal cliente finale alla velocità massima di 2000 pollici al minuto (IPM) su superfici complesse rampate. Tutte le giaciture possono essere eseguite in modo totalmente bidirezionale e con controllo dell’operatore sulla velocità di avanzamento senza effetti sulla precisione del taglio finale. Electroimpact è un fornitore di elevata esperienza di soluzioni di automazione di fabbrica ed attrezzaggio. Il punto di forza dell’azienda è l’integrazione di automazione ed attrezzaggio in soluzioni di produzione sinergiche. Team ingegneristici ad alta esperienza permettono di gestire con flessibilità più grandi progetti contemporaneamente. Questo approccio unico ha fatto sì che Electroimpact sia cresciuta fino a diventare il maggiore integratore di linee di assemblaggio aeronautiche a livello mondiale. La base clienti include produttori di aeromobili commerciali e militari in tutto il mondo.
Il cliente più recente è un grosso costruttore statunitense di componenti per aeromobili, che produce fusoliere, componenti sotto-ala, compositi e ali per l’industria aeronautica. La sede centrale dell’azienda è a Wichita, Kansas, la Capitale Aeronautica del Mondo, con altri stabilimenti a Tulsa e McAlester, Oklahoma, Prestwick, Scozia, e Samlesbury, inghilterra.
La macchina Automated Fiber Placement (AFP) è stata progettata per produrre grandi strutture per aeromobili commerciali ed è caratterizzata da teste a cambio rapido totalmente modulari, con cambio automatico della testa in 30 secondi. Per potere produrre queste grandi parti aerospaziali, la struttura della macchina che controlla i movimenti X, Y e Z della testa di giacitura della fibra (Post Mill o Gantry Designs) pesa 350.000 libbre (175 tonnellate) ed è accelerata a 0,2 g. I tow di fibra di carbonio (sottili strisce di fibra di carbonio impregnata) sono piazzate su forme materiali multiple sulla stessa parte (tow larghi 1/4" o 1/8" in aree a elevate contornature, 1/2" o più in aree a basse contornature) per la massima produttività possibile: si tratta di un’operazione al 100% senza torsione, al 100% senza rottura delle giunzioni e totalmente bidirezionale.
Gli assi X, Y, Z e di rotazione del tamburo funzionano insieme per consentire alla fibra di carbonio di seguire il contorno della parte in produzione. I tow di fibra di carbonio sono piazzati sull’utensile che è lavorato nella forma della parte finale. Inoltre, la fibra di carbonio deve essere applicata in strati differenti e in direzioni differenti per ottimizzare la robustezza della parte finale. Il fatto è che la fibra di carbonio è molto resistente alla trazione, quindi tutti i carichi che agiscono sulla parte devono essere supportati in trazione.
Le corse possono variare da brevi ~ 2 metri (6,6 piedi.) di corsa sull’asse X, fino alla corsa massima sull’asse X, pari a ~30 metri (98,4 piedi). La corsa dipende dalla parte in produzione.
Un sistema di controllo avanzato
Questa macchina ha richiesto una completa reingegnerizzazione del sistema di taglio e l’ottimizzazione del sistema di avanzamento, del percorso dei tow e del sistema a rastrelliera della testa di giacitura della fibra. Il sistema di controllo della macchina ha rispettato le specifiche di taglio e di aggiunta al volo a 2000 IPM e oltre. In particolare, dal taglio al volo ad alta velocità è nata una serie di problemi. Con una velocità di giacitura di 2000 IPM (R) e una tolleranza di giacitura del taglio finale di +/-0,050" (o 0,10" totale [k]), la finestra di opportunità nel tempo è la seguente:
T = (60 * k) / R (secondi), ossia
T = (60 * 0,10) / 2000T = 0,003 secondi.
In altri termini, a 2000 IPM, 1 millisecondo equivale a 0,033 pollici di spostamento del tow. Ciò indica che la precisione e ripetibilità totale del sistema di taglio deve essere molto migliore della tipica velocità di scansione di un tipico CNC (4 - 8 ms). La ripetibilità dei singoli componenti (per es. attuatori, valvole, ecc.) deve essere nel range del sub-millisecondo o migliore. Inoltre, il sistema di segnalazione di un taglio deve avere una risoluzione del sub-millisecondo.
Electroimpact ha sviluppato un meccanismo di taglio ad alta velocità che permette di tagliare a velocità elevate con tempi di taglio totali minori di 1 millisecondo. Il sistema ha anche una piccolissima variabilità, rendendo precisa e ripetibile il piazzamento dei tow anche a elevatissime velocità di giacitura. I fattori che influenzano i tempi del taglio e dell’aggiunta al volo includono l’esecuzione del programma, la reazione del modulo d’uscita, l’attuazione delle valvole a solenoide, le reazioni del flusso d’aria e inerziali dei meccanismi di attuazione, ecc. Ciascuno di questi fattori provoca un ritardo nell’esecuzione di un taglio o di un’aggiunta rispetto al segnale nominale. Se il ritardo è prevedibile e ripetibile, il tempo di taglio può essere compensato. Questi ritardi devono altresì essere minimizzati laddove è possibile. Grazie ad ampi sviluppi e collaudi presso Electroimpact, la variabilità dei ritardi di avanzamento e taglio è stata ridotta a meno di 1 millisecondo, rendendo molto preciso a velocità elevate il piazzamento di fine taglio o inizio sequenza.
I controllori convenzionali come i PLC o i CNC generalmente funzionano sulla base di un “tempo di scansione”, che tipicamente viene misurato in millisecondi. Le uscite sono attuate una volta per scansione, limitando quindi la risoluzione di tempo al tempo di scansione. Se un ritardo di 1 millisecondo si traduce in un errore di giacitura finale di 0,033" a 2000"/minuto, introdurre un errore di controllo anche di 1 millisecondo sarebbe inaccettabile per tagli o aggiunte al volo ad alta velocità. E’ necessaria un’integrazione estremamente stretta del controllo di moto CNC e dei tempi dei comandi di taglio e aggiunta per ridurre al minimo i ritardi di tempo del controllo.
Electroimpact ha scelto di utilizzare una "Customer Board" Fanuc, un sistema che le ha permesso di interpolare il taglio e l’aggiunta nel profilo di moto al livello del comando di velocità del CNC. Questa è la prima implementazione della customer board all’esterno del Giappone ed Electroimpact ha lavorato a stretto contatto con Fanuc per implementare caratteristiche specifiche per applicazioni AFP. I ritardi di tempo indotti dal controllo sono nel range dei microsecondi, eliminando effettivamente i ritardi dei tempi di controllo come sorgente di errori nel taglio e nell’aggiunta.
I clienti di Electroimpact hanno riconosciuto la necessità che il software di programmazione fosse fornito da un produttore di software riconosciuto dall’industria come parte di una suite standard di software aggiornato e mantenuto regolarmente. Per oltre 2 anni, Electroimpact ha avuto una partnership non esclusiva con CGTech per sviluppare il software di programmazione AFP denominato "Vericut Composite Programming and Simulation Suite".
La soluzione unica di ANDANTEX
Per Electroimpact, ANDANTEX USA ha affrontato i vincoli più difficili: combinare le alte velocità e gli enormi pesi delle macchine con moti molto complessi, caratterizzati da accelerazioni successive e frequenti in tutte le direzioni.
"Abbiamo scelto Andantex perché nessun altro produce una scatola di precisione in quella gamma di coppie e spinte", spiega Peter Vogeli, Ingegnere Capo di ElectroImpact, Inc.
Il primo problema è quello di eliminare il gioco. I sistemi di azionamento a pignone e cremagliera TwinDRIVE sono composti da due servoriduttori planetari montati in parallelo che sono accoppiati elettricamente. Questo sistema di precarico elimina il gioco e permette al servosistema di controllare con precisione la posizione degli assi.
Il secondo problema è assicurare la massima rigidità per offrire una perfetta ripetibilità nonostante la frequente accelerazione. Un’estrema rigidità è ottenuta in tutte le direzioni grazie a un albero d’uscita con pignone integrato supportato da cuscinetti d’uscita rinforzati. Questo concetto unico di REDEX ANDANTEX offre caratteristiche di rigidità torsionale che sono tra le migliori sul mercato ma, soprattutto, offre un’eccezionale rigidità lungo gli altri piani (radiale e assiale) (**vedere se Redex può sviluppare uno schizzo che mostri i piani di deflessione torsionale, radiale ed assiale**); ciò permette spesso l’uso di valori di accelerazione o peso quasi doppi rispetto ad altre soluzioni. Questo progetto esclusivo combina cuscinetti d’uscita fortemente rinforzati con pignoni integrati all’albero d’uscita (induriti superficialmente e rettificati, con lo stesso diametro dell’albero). Il diametro primitivo del pignone è ottimizzato per assicurare il rapporto migliore fra la coppia trasmessa e la rigidità dal punto di vista della cremagliera. La disposizione stessa dei cuscinetti consiste di due cuscinetti a rulli conici, precaricati e generosamente sovradimensionati. Questa disposizione dei cuscinetti è stata progettata per supportare il pignone il più vicino possibile alla forza applicata, con il solo spessore del controdado a separare il pignone dal cuscinetto d’uscita. Questo particolare progetto offre una considerevole riduzione della deflessione radiale, che è la causa del 60% della deflessione complessiva ma che è raramente affrontata in modo soddisfacente da altri sistemi.
Andantex USA è il fornitore ‘one stop’ di riduttori, cremagliere e pignoni ad assi lineari e rotanti
Le apparecchiature ANDANTEX sono installate su tutti gli assi, creando una responsabilità unica nel comportamento meccanico globale della macchina.
L’asse di rotazione del tamburo aziona l’utensile sul quale la fibra di carbonio viene depositata. L’utensile è tipicamente realizzato in invar, un tipo di acciaio con bassissimo tasso di espansione termica. Ciò è importante perché, una volta realizzata la parte, l’intero assemblato è messo in un autoclave e cotto per essere sicuri che la fibra di carbonio impregnata vulcanizzi nel suo stato finale. Dopo la rimozione dell’utensile, la parte rimanente viene completamente realizzata in fibra di carbonio. 4 KRP taglia 6 permettono la rotazione precisa.
- Velocità rotativa massima: 81 giri/min
- Velocità rotativa nominale: 25 giri/min
- Coppia di picco: 6600 Nm
- Configurazione: (2) Twin Drives/asse
L’asse X è equipaggiato con 4 riduttori planetari KRP taglia 6, la taglia più grande disponibile nella gamma REDEX ANDANTEX. Essi ingranano con due cremagliere lunghe 35 m.
- Velocità lineare = 51 m/min. (2000 pollici/min)
- Massa = 160 tonnellate (175 tonnellate US)
- Accelerazione = 0,2 g
- Configurazione: (2) TwinDRIVES/asse
L’asse Y è equipaggiato con 2 riduttori planetari SRP in configurazione TwinDRIVE. Essi sono montati su 5,5m di cremagliera
- Velocità lineare = 53 m/min. (2450 pollici/min.)
- Massa = 14,3 tonnellate (15,7 tonnellate US)
- Accelerazione = 0,2 g
- Configurazione: (1) TwinDRIVE/asse
Per il feedback dell’encoder secondario sugli assi X e Y, Electroimpact utilizza anche il PDP ‘Pignone splittato’ di Andantex per pilotare l’encoder direttamente dalla cremagliera con gioco nullo. Questa soluzione conveniente è la prima generazione di ‘Doppio pignone precaricato’ per applicazioni a pignone e cremagliera di elevata precisione. Il PDP è composto da 2 pignoni WMH rettificati, ciascuno pari a ½ della larghezza della cremagliera, connessi tra loro tramite un sistema di precarico brevettato per eliminare il gioco di accoppiamento fra cremagliera e pignone. (** immagine del PDP picture **). Il concetto innovativo del PDP fornisce il feedback dell’encoder direttamente dalla cremagliera, assicurando un’elevata precisione e ripetibilità di posizionamento a costi molto competitivi.
- Asse X Mod. 10, Circ. = 500 mm
- Asse Y Mod. 5, Circ. = 250 mm
Infine, Andantex ha fornito ad Electroimpact una cremagliera elicoidale indurita superficialmente e rettificata in moduli 10 & 5 per gli assi X e Y insieme a pignoni di lubrificazione in schiuma di poliuretano per rilubrificare automaticamente le cremagliere. Le cremagliere sono fornite in sezioni di 1 (o 2) metri e progettate per essere collegate da estremo a estremo in modo da creare la lunghezza richiesta per l’asse. Ciò significa che Andantex può fornire tutti i componenti meccanici fra il servomotore e l’asse.
“Alla fine, la precisione di piazzamento è uguale alla precisione di taglio (+/- 0,050”) alla massima velocità. Gli assi azionati dai riduttori Redex Andantex devono avere una precisione maggiore di questo valore, perché lavorano insieme per formare una forma complessa. Possiamo stimare che la precisione degli assi X, Y e Z sia 1/10 della precisione di piazzamento o +/- 0,005” (0.0125 mm)”, spiega Dave Regiec, project manager di ANDANTEX.
Il cliente più recente è un grosso costruttore statunitense di componenti per aeromobili, che produce fusoliere, componenti sotto-ala, compositi e ali per l’industria aeronautica. La sede centrale dell’azienda è a Wichita, Kansas, la Capitale Aeronautica del Mondo, con altri stabilimenti a Tulsa e McAlester, Oklahoma, Prestwick, Scozia, e Samlesbury, inghilterra.
La macchina Automated Fiber Placement (AFP) è stata progettata per produrre grandi strutture per aeromobili commerciali ed è caratterizzata da teste a cambio rapido totalmente modulari, con cambio automatico della testa in 30 secondi. Per potere produrre queste grandi parti aerospaziali, la struttura della macchina che controlla i movimenti X, Y e Z della testa di giacitura della fibra (Post Mill o Gantry Designs) pesa 350.000 libbre (175 tonnellate) ed è accelerata a 0,2 g. I tow di fibra di carbonio (sottili strisce di fibra di carbonio impregnata) sono piazzate su forme materiali multiple sulla stessa parte (tow larghi 1/4" o 1/8" in aree a elevate contornature, 1/2" o più in aree a basse contornature) per la massima produttività possibile: si tratta di un’operazione al 100% senza torsione, al 100% senza rottura delle giunzioni e totalmente bidirezionale.
Gli assi X, Y, Z e di rotazione del tamburo funzionano insieme per consentire alla fibra di carbonio di seguire il contorno della parte in produzione. I tow di fibra di carbonio sono piazzati sull’utensile che è lavorato nella forma della parte finale. Inoltre, la fibra di carbonio deve essere applicata in strati differenti e in direzioni differenti per ottimizzare la robustezza della parte finale. Il fatto è che la fibra di carbonio è molto resistente alla trazione, quindi tutti i carichi che agiscono sulla parte devono essere supportati in trazione.
Le corse possono variare da brevi ~ 2 metri (6,6 piedi.) di corsa sull’asse X, fino alla corsa massima sull’asse X, pari a ~30 metri (98,4 piedi). La corsa dipende dalla parte in produzione.
Un sistema di controllo avanzato
Questa macchina ha richiesto una completa reingegnerizzazione del sistema di taglio e l’ottimizzazione del sistema di avanzamento, del percorso dei tow e del sistema a rastrelliera della testa di giacitura della fibra. Il sistema di controllo della macchina ha rispettato le specifiche di taglio e di aggiunta al volo a 2000 IPM e oltre. In particolare, dal taglio al volo ad alta velocità è nata una serie di problemi. Con una velocità di giacitura di 2000 IPM (R) e una tolleranza di giacitura del taglio finale di +/-0,050" (o 0,10" totale [k]), la finestra di opportunità nel tempo è la seguente:
T = (60 * k) / R (secondi), ossia
T = (60 * 0,10) / 2000T = 0,003 secondi.
In altri termini, a 2000 IPM, 1 millisecondo equivale a 0,033 pollici di spostamento del tow. Ciò indica che la precisione e ripetibilità totale del sistema di taglio deve essere molto migliore della tipica velocità di scansione di un tipico CNC (4 - 8 ms). La ripetibilità dei singoli componenti (per es. attuatori, valvole, ecc.) deve essere nel range del sub-millisecondo o migliore. Inoltre, il sistema di segnalazione di un taglio deve avere una risoluzione del sub-millisecondo.
Electroimpact ha sviluppato un meccanismo di taglio ad alta velocità che permette di tagliare a velocità elevate con tempi di taglio totali minori di 1 millisecondo. Il sistema ha anche una piccolissima variabilità, rendendo precisa e ripetibile il piazzamento dei tow anche a elevatissime velocità di giacitura. I fattori che influenzano i tempi del taglio e dell’aggiunta al volo includono l’esecuzione del programma, la reazione del modulo d’uscita, l’attuazione delle valvole a solenoide, le reazioni del flusso d’aria e inerziali dei meccanismi di attuazione, ecc. Ciascuno di questi fattori provoca un ritardo nell’esecuzione di un taglio o di un’aggiunta rispetto al segnale nominale. Se il ritardo è prevedibile e ripetibile, il tempo di taglio può essere compensato. Questi ritardi devono altresì essere minimizzati laddove è possibile. Grazie ad ampi sviluppi e collaudi presso Electroimpact, la variabilità dei ritardi di avanzamento e taglio è stata ridotta a meno di 1 millisecondo, rendendo molto preciso a velocità elevate il piazzamento di fine taglio o inizio sequenza.
I controllori convenzionali come i PLC o i CNC generalmente funzionano sulla base di un “tempo di scansione”, che tipicamente viene misurato in millisecondi. Le uscite sono attuate una volta per scansione, limitando quindi la risoluzione di tempo al tempo di scansione. Se un ritardo di 1 millisecondo si traduce in un errore di giacitura finale di 0,033" a 2000"/minuto, introdurre un errore di controllo anche di 1 millisecondo sarebbe inaccettabile per tagli o aggiunte al volo ad alta velocità. E’ necessaria un’integrazione estremamente stretta del controllo di moto CNC e dei tempi dei comandi di taglio e aggiunta per ridurre al minimo i ritardi di tempo del controllo.
Electroimpact ha scelto di utilizzare una "Customer Board" Fanuc, un sistema che le ha permesso di interpolare il taglio e l’aggiunta nel profilo di moto al livello del comando di velocità del CNC. Questa è la prima implementazione della customer board all’esterno del Giappone ed Electroimpact ha lavorato a stretto contatto con Fanuc per implementare caratteristiche specifiche per applicazioni AFP. I ritardi di tempo indotti dal controllo sono nel range dei microsecondi, eliminando effettivamente i ritardi dei tempi di controllo come sorgente di errori nel taglio e nell’aggiunta.
I clienti di Electroimpact hanno riconosciuto la necessità che il software di programmazione fosse fornito da un produttore di software riconosciuto dall’industria come parte di una suite standard di software aggiornato e mantenuto regolarmente. Per oltre 2 anni, Electroimpact ha avuto una partnership non esclusiva con CGTech per sviluppare il software di programmazione AFP denominato "Vericut Composite Programming and Simulation Suite".
La soluzione unica di ANDANTEX
Per Electroimpact, ANDANTEX USA ha affrontato i vincoli più difficili: combinare le alte velocità e gli enormi pesi delle macchine con moti molto complessi, caratterizzati da accelerazioni successive e frequenti in tutte le direzioni.
"Abbiamo scelto Andantex perché nessun altro produce una scatola di precisione in quella gamma di coppie e spinte", spiega Peter Vogeli, Ingegnere Capo di ElectroImpact, Inc.
Il primo problema è quello di eliminare il gioco. I sistemi di azionamento a pignone e cremagliera TwinDRIVE sono composti da due servoriduttori planetari montati in parallelo che sono accoppiati elettricamente. Questo sistema di precarico elimina il gioco e permette al servosistema di controllare con precisione la posizione degli assi.
Il secondo problema è assicurare la massima rigidità per offrire una perfetta ripetibilità nonostante la frequente accelerazione. Un’estrema rigidità è ottenuta in tutte le direzioni grazie a un albero d’uscita con pignone integrato supportato da cuscinetti d’uscita rinforzati. Questo concetto unico di REDEX ANDANTEX offre caratteristiche di rigidità torsionale che sono tra le migliori sul mercato ma, soprattutto, offre un’eccezionale rigidità lungo gli altri piani (radiale e assiale) (**vedere se Redex può sviluppare uno schizzo che mostri i piani di deflessione torsionale, radiale ed assiale**); ciò permette spesso l’uso di valori di accelerazione o peso quasi doppi rispetto ad altre soluzioni. Questo progetto esclusivo combina cuscinetti d’uscita fortemente rinforzati con pignoni integrati all’albero d’uscita (induriti superficialmente e rettificati, con lo stesso diametro dell’albero). Il diametro primitivo del pignone è ottimizzato per assicurare il rapporto migliore fra la coppia trasmessa e la rigidità dal punto di vista della cremagliera. La disposizione stessa dei cuscinetti consiste di due cuscinetti a rulli conici, precaricati e generosamente sovradimensionati. Questa disposizione dei cuscinetti è stata progettata per supportare il pignone il più vicino possibile alla forza applicata, con il solo spessore del controdado a separare il pignone dal cuscinetto d’uscita. Questo particolare progetto offre una considerevole riduzione della deflessione radiale, che è la causa del 60% della deflessione complessiva ma che è raramente affrontata in modo soddisfacente da altri sistemi.
Andantex USA è il fornitore ‘one stop’ di riduttori, cremagliere e pignoni ad assi lineari e rotanti
Le apparecchiature ANDANTEX sono installate su tutti gli assi, creando una responsabilità unica nel comportamento meccanico globale della macchina.
L’asse di rotazione del tamburo aziona l’utensile sul quale la fibra di carbonio viene depositata. L’utensile è tipicamente realizzato in invar, un tipo di acciaio con bassissimo tasso di espansione termica. Ciò è importante perché, una volta realizzata la parte, l’intero assemblato è messo in un autoclave e cotto per essere sicuri che la fibra di carbonio impregnata vulcanizzi nel suo stato finale. Dopo la rimozione dell’utensile, la parte rimanente viene completamente realizzata in fibra di carbonio. 4 KRP taglia 6 permettono la rotazione precisa.
- Velocità rotativa massima: 81 giri/min
- Velocità rotativa nominale: 25 giri/min
- Coppia di picco: 6600 Nm
- Configurazione: (2) Twin Drives/asse
L’asse X è equipaggiato con 4 riduttori planetari KRP taglia 6, la taglia più grande disponibile nella gamma REDEX ANDANTEX. Essi ingranano con due cremagliere lunghe 35 m.
- Velocità lineare = 51 m/min. (2000 pollici/min)
- Massa = 160 tonnellate (175 tonnellate US)
- Accelerazione = 0,2 g
- Configurazione: (2) TwinDRIVES/asse
L’asse Y è equipaggiato con 2 riduttori planetari SRP in configurazione TwinDRIVE. Essi sono montati su 5,5m di cremagliera
- Velocità lineare = 53 m/min. (2450 pollici/min.)
- Massa = 14,3 tonnellate (15,7 tonnellate US)
- Accelerazione = 0,2 g
- Configurazione: (1) TwinDRIVE/asse
Per il feedback dell’encoder secondario sugli assi X e Y, Electroimpact utilizza anche il PDP ‘Pignone splittato’ di Andantex per pilotare l’encoder direttamente dalla cremagliera con gioco nullo. Questa soluzione conveniente è la prima generazione di ‘Doppio pignone precaricato’ per applicazioni a pignone e cremagliera di elevata precisione. Il PDP è composto da 2 pignoni WMH rettificati, ciascuno pari a ½ della larghezza della cremagliera, connessi tra loro tramite un sistema di precarico brevettato per eliminare il gioco di accoppiamento fra cremagliera e pignone. (** immagine del PDP picture **). Il concetto innovativo del PDP fornisce il feedback dell’encoder direttamente dalla cremagliera, assicurando un’elevata precisione e ripetibilità di posizionamento a costi molto competitivi.
- Asse X Mod. 10, Circ. = 500 mm
- Asse Y Mod. 5, Circ. = 250 mm
Infine, Andantex ha fornito ad Electroimpact una cremagliera elicoidale indurita superficialmente e rettificata in moduli 10 & 5 per gli assi X e Y insieme a pignoni di lubrificazione in schiuma di poliuretano per rilubrificare automaticamente le cremagliere. Le cremagliere sono fornite in sezioni di 1 (o 2) metri e progettate per essere collegate da estremo a estremo in modo da creare la lunghezza richiesta per l’asse. Ciò significa che Andantex può fornire tutti i componenti meccanici fra il servomotore e l’asse.
“Alla fine, la precisione di piazzamento è uguale alla precisione di taglio (+/- 0,050”) alla massima velocità. Gli assi azionati dai riduttori Redex Andantex devono avere una precisione maggiore di questo valore, perché lavorano insieme per formare una forma complessa. Possiamo stimare che la precisione degli assi X, Y e Z sia 1/10 della precisione di piazzamento o +/- 0,005” (0.0125 mm)”, spiega Dave Regiec, project manager di ANDANTEX.
Richiedi maggiori informazioni…