www.industria-online.com
05
'18
Written on Modified on
Libera le possibilità offerte dalla lavorazione additiva con la produttività dei laser multipli
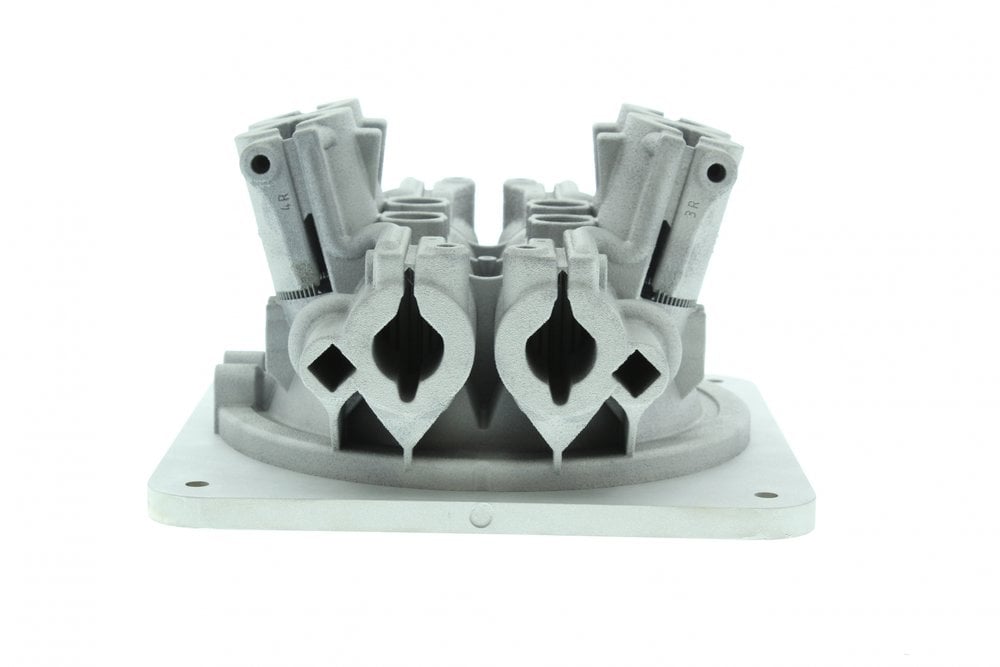
Accelerando il processo fino a quattro volte, Renishaw prevede che la RenAM 500Q possa rendere ancora più appetibile la stampa 3D in metallo e portare questa tecnologia in applicazioni dove risultava fino ad ora troppo costosa, nonché in nuovi settori che ancora non l'hanno incorporata nei processi produttivi.
Progettazione innovativa grazie all'additive manufacturing
Il fattore chiave per la RenAM 500Q è il nuovo ed innovativo sistema ottico. Questo componente fondamentale è nato dalla stretta collaborazione tra vari reparti di progettazione all'interno di Renishaw: meccanica software e sistemi di controllo.
Una volta entrati nel gruppo ottico, i fasci dei laser a fibra d'itterbio vengono guidati da quattro coppie di specchi comandati da galvanometri di precisione (galvo), che ruotano per orientare i fasci laser sulla piastra di lavoro. Inoltre, il sistema ottico varia dinamicamente le lunghezze focali dei laser al fine di mantenere costante la dimensione del fascio al variare dell'angolo di emissione. Garantire la precisione sul letto di polvere richiede grande competenza nel campo dell'ottica e del controllo; proprio quella che Renishaw ha perfezionato in anni di lavoro con prodotti come il sistema di misura a 5 assi REVO® per macchine di misura a coordinate.
Renishaw ha sfruttato le proprie capacità in-house di produzione additiva (AM) per produrre il sistema ottico della RenAM 500Q. Avvalersi dell'AM per produrre questo componente ha consentito a Renishaw di ridurre l'ingombro degli specchi di guida, nonché di incorporare canali di raffreddamento interni per mantenere un'accurata stabilità termica. Grazie a queste innovazioni portate dall'utilizzo dell'AM in produzione, Renishaw ha potuto realizzare una macchina che affronta con successo la sfida di migliorare la produttività delle macchine di medie dimensioni, quelle più diffuse.
Il design del sistema ottico viene prodotto tramite una tecnica di produzione mista; incorporare la piastra di lavorazione, generalmente scartata, nel componente finale ha consentito di ridurre il volume del materiale da stampare e di eliminare la fase di rimozione dei componenti dalla piastra. Il Solution Center Renishaw ha ottimizzato ulteriormente il componente, la struttura di supporto e la progettazione DFM per la produzione in serie.
Produttività senza vincoli
Il nuovo sistema a quattro laser migliora la produttività fino a quattro volte, senza aumentare le dimensioni della piattaforma. I sistemi più grandi devono affrontare sfide aggiuntive, come le maggiori quantità di materiale richieste ad inventario, la manipolazione meccanica di piastre più pesanti, l'efficienza del gas di schermatura su un'area di lavoro più estesa, nonché gli inevitabili costi di investimento maggiori con ingombri più elevati. Per i componenti più grandi questi compromessi devono essere accettati, ma in termini di attrattività sono le macchine di medie dimensioni a risultare più interessanti, anche se risentivano in passato di una minore produttività a causa del numero limitato di laser.
La RenAM 500Q sfrutta l'architettura del sistema monolaser RenAM 500M di Renishaw per la produzione di serie, ma con alcune differenze significative. La più evidente è la presenza di quattro laser, che comporta la riprogettazione di tutti i sottosistemi al fine di stare al passo con la maggiore produttività offerta. Fondamentale è la capacità di gestire le emissioni di processo aggiuntive generate da quattro laser. Risolvere il problema aumentando l'erogazione di gas e la sua velocità carica maggiormente altri sottosistemi, come quello di filtraggio utilizzato per catturare le emissioni di processo. In questo caso, Renishaw ha aggiunto un intercooler nel flusso del gas che mantiene le temperature di processo stabili e un pre-filtro a ciclone che separa le particelle più piccole da quelle più grandi per salvaguardare la durata del filtro e aumentare il riutilizzo delle polveri.
Tra i vari miglioramenti trova sicuramente spazio l'ottimizzazione del flusso di gas nell'area di lavorazione per ridurre significativamente le pulizie tra due cicli di lavoro successivi. Con quattro laser che fondono materiale sull'intera area di lavoro, è però fondamentale mantenere anche una relazione precisa tra il sistema ottico e il letto di polvere. Diverse innovazioni contribuiscono al raggiungimento di questo risultato, tra cui i supporti cinematici utilizzati per posizionare il distributore, i quali migliorano i tempi di set-up e la ripetibilità.
Ingombro ridotto, grandi possibilità
Utilizzare quattro laser con efficienza richiede più lavoro preventivo in termini di programmazione ed ingegnerizzazione del processo. Il modo più semplice è partire assegnando ciascun laser a un singolo componente o a un gruppo di componenti indipendenti. I laser possono quindi lavorare in parallelo. I primi risultati suggeriscono che sia necessario prestare una certa attenzione se la lavorazione viene effettuata simultaneamente su componenti adiacenti, poiché le emissioni di uno possono avere effetti sull'altro. Complessivamente questo è lo scenario di lavorazione più semplice da gestire ed è il punto d'inizio suggerito per gran parte degli utenti.
Al di là di questo, è l'applicazione a giocare un ruolo più significativo nelle scelte correlate alla lavorazione con laser multipli. Ovviamente, è possibile utilizzare tutti e quattro i laser per lavorare su un singolo componente, e la capacità del sistema Renishaw di lavorare sull'intero letto di polvere con ciascun laser consente di ottimizzare al massimo la strategia di lavorazione.
Ne è un esempio il blocco dei galvanometri della RenAM 500Q, che viene prodotto tramite lavorazione additiva in 19 ore utilizzando quattro laser. Si tratta di un componente AM ideale, nonché di un'applicazione le cui necessità operative sono focalizzate sulla stabilità termica, l'eliminazione delle perdite e la ripetibilità geometrica. Non è sottoposto a carichi strutturali significativi, quindi le verifiche sul componente possono limitarsi ai requisiti di funzionalità progettuale.
Per i componenti più esigenti dal punto vista strutturale, specialmente nel caso di applicazioni dove la sicurezza è critica, come nel settore aerospaziale, sanitario o dei veicoli sportivi, gran parte degli utenti vorrà approfondire gli effetti legati all'interazione tra i laser multipli; saranno quindi necessarie prove e valutazioni più estese, che possono essere garantite dal programma di accesso ai Solution Center Renishaw.
Ciascun utente avrà il proprio punto di vista su come avvicinarsi alla tecnologia con laser multipli: se utilizzarla per aumentare la produttività in un'applicazione AM già matura, oppure per sbloccare nuovi mercati e nuove applicazioni grazie ai notevoli miglioramenti in termini di produttività.
La lavorazione additiva diventa quindi una tecnologia utilizzabile anche per la produzione in serie, destinata a diffondersi anche in applicazioni in cui non siano solo i vantaggi tecnici a risultare interessanti, ma anche i benefici economici per la realizzazione di componenti di alta qualità.
Inoltre, il sistema RenAM 500Q di Renishaw offre una produttività fino a quattro volte maggiore con un aumento modesto dell'investimento iniziale, questo significa ridurre il costo del singolo componente per ogni lotto, accrescere la possibilità di investire sulla stampa 3D in metallo e offrire vantaggi addizionali agli utenti esistenti. Per rispondere alla domanda iniziale, pare proprio che quattro laser siano effettivamente meglio di uno.
www.renishaw.it
Richiedi maggiori informazioni…