www.industria-online.com
26
'15
Written on Modified on
4 telecamere per controllare le ganasce dei freni
Una macchina realizzata da Bonetto Automazioni controlla con precisione la qualità di componenti fondamentali per la sicurezza stradale.
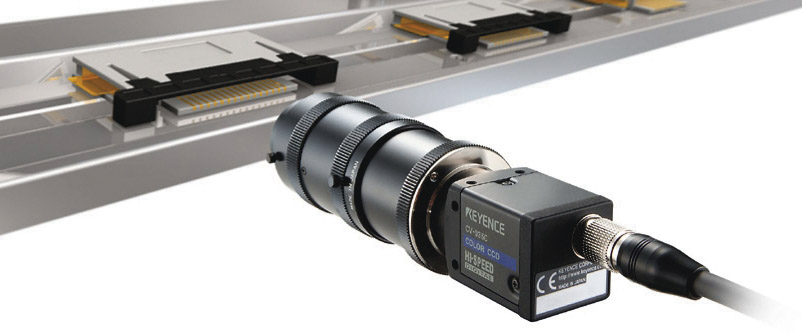
Passando a tempi più recenti, da circa 20 anni, il Gruppo Bonetto è entrato pienamente nel campo dell’automazione, occupandosi prevalentemente del settore automotive. In generale, il core business è quello dell’assemblaggio di parti. Dopo avere iniziato con la produzione di linee di finitura per pastiglie freno, il Gruppo Bonetto è passato alle macchine speciali per l’assemblaggio di componenti della pompa gasolio e della pompa del vuoto, del gruppo frenante e di altre parti del veicolo.
Oggi, il Gruppo Bonetto si occupa di tutte le fasi che vanno dalla progettazione meccanica delle macchine speciali costruite insieme al cliente, alla gestione delle aziende esterne che eseguono le lavorazioni meccaniche, all’assemblaggio dei componenti, all’impiantizzazione e alla messa in funzione delle macchine.
Dall’idea al prodotto finale
Si.El., la società che rappresenta il Dipartimento Elettrico e Software del Gruppo Bonetto. opera da oltre 15 anni nei più svariati settori dell’impiantistica elettrica, automazione e servizi per l’energia come fornitore di impianti e servizi.
“Si.El. sviluppa la progettazione elettrica e del software, la costruzione dei quadri, fino alla messa in funzione e alla consegna ‘chiavi in mano’ al cliente”, riferisce l’ingegner Stefano Fenoglio, Responsabile del Gruppo Software e della messa in funzione degli impianti di Si.El.
Recentemente, Si.El ha portato a termine per il Gruppo Bonetto la realizzazione di una nuova macchina di finitura delle ganasce freno per veicoli industriali. “Da molti anni siamo presenti nel settore dei materiali di attrito e delle ganasce in particolare”, sottolinea l’ing. Fenoglio. “In particolare, il cliente ci ha richiesto una macchina di rettifica delle ganasce che, provenendo dagli stampi, non hanno ancora una forma perfettamente circolare. Deve quindi essere eseguita una lavorazione di rettifica per regolare la circonferenza della ganascia, seguita dal controllo qualità del pezzo”.
Una macchina con due tavole
La prima parte della macchina comprende due grosse mole e un sistema robotizzato che carica le ganasce da un alimentatore. Infatti, le ganasce vengono ricevute impilate a gruppi di 30-40 unità su un sistema di trasporto, per offrire un buffer di lavoro all’operatore. Il robot carica quindi la ganascia sulla prima tavola rotante che la porta sotto la prima mola, dove viene eseguita una sgrossatura su tutta la sua circonferenza. Successivamente la tavola ruota e porta la ganascia sotto la seconda mola, che esegue una finitura superficiale in modo da ottenere il diametro richiesto. A questo punto il robot preleva la ganascia e la sposta sulla seconda tavola rotante per potere eseguire una serie di controlli. In particolare, le prime due postazioni, di controllo metrico, misurano tramite tastatori alcune quote meccaniche del pezzo come raggio assoluto, raggio polare, parallelismo e così via. Nelle due postazioni successive sono state invece installati sistemi di visione Keyence che verificano una serie di caratteristiche di qualità del prodotto in base alle esigenze del cliente: la geometria di tutti i fori e delle asole, l’altezza e la larghezza delle alette della ganascia, la marcatura sul lining con distinzione del colore blu/bianco/rosso (tre tipi di ganasce), il punto di attacco fascia e il punto di attacco lining, la presenza e l’area tempra, fino alla presenza della luce fascia/costa. In particolare, la presenza di luce fra due lamiere saldate è motivo di scarto del pezzo.
“I dispositivi Keyence sono stati programmati in modo che vengano eseguiti tutti i controlli specifici al pezzo che viene disposto sulla tavola dal robot, cambiando la combinazione di misure e controlli quando si presenta un pezzo di tipo diverso”, spiega l’ingegner Fenoglio. “Dopo questi controlli, la macchina scarta automaticamente i pezzi fuori tolleranza”.
Configurazione
La configurazione della macchina prevede quindi, nella prima stazione di controllo, una telecamera Keyence da 5MP e 1 telecamera da 2MP Front light con 4 barre LED e 1 backlight per la verifica geometrie fori e asole, il controllo dimensionale alette, il controllo del punto d’attacco fascia e del punto d’attacco lining in backlight e la verifica presenza e area tempra. Nella seconda stazione di controllo sono presenti due telecamere da 2MP, un sensore di visione IVG e due backlight per la verifica presenza luce fascia/costa e il controllo presenza e colore marcatura.
La macchina utilizza l’algoritmo ShapeTrax2 (ricerca della forma geometrica), un algoritmo di ispezione delle macchie, la funzione di tendenza posizione bordi e la funzione di tendenza larghezza bordi.
La misurazione geometrica dimensionale che richiede l’uso di molti strumenti e calcoli complessi può essere impostata con un clic. Dato che le impostazioni sono semplici, lo strumento geometrico/dimensionale non solo riduce le ore di lavoro ma consente di portare grandi vantaggi anche dal punto di vista operativo. Infine, la correzione dell’ombreggiatura in tempo reale corregge le gradazioni cromatiche nell’area di ispezione in tempo reale. Completa la configurazione la generazione automatica del manuale per l’utente.
Una scelta naturale
“Keyence è un nostro fornitore storico, soprattutto nel settore della sensoristica”, afferma l’ingegner Fenoglio. “In passato utilizzavamo i sistemi di visione di altre aziende ma, dopo avere avuto la possibilità di provare i dispositivi e il servizio Keyence su altre applicazioni particolarmente impegnative, abbiamo deciso di affidarci a questo fornitore, avendo ottenuto un’ottima risposta in termini sia tecnici che commerciali. Il service Keyence ci segue infatti dalla fase di campionatura iniziale, alla messa in funzione presso il nostro stabilimento, alla consegna della macchina al cliente, alla messa in funzione finale presso il cliente. Anche la nostra richiesta di variazione in corsa del progetto ha ricevuto una risposta estremamente tempestiva, permettendo una consegna puntuale al cliente finale”.
Il sistema di visione è unico ma utilizza più telecamere per coprire tutta l’area di lavoro. “Abbiamo anche constatato che non era possibile utilizzare una sola postazione di lavoro perché i diversi controlli richiedevano condizioni diverse e non era possibile alloggiare più telecamere con ottiche così differenti nella stessa postazione. Quindi, le 14 prove che vengono eseguite sono state assegnate a due postazioni diverse”, spiega l’ingegner Fenoglio. Questo ha portato a 4 il numero totale delle telecamere. Quindi, nella prima postazione ci sono 2 telecamere e un sistema di visione IVG per alcune delle prove, oltre al controllore che gestisce l’illuminazione frontale e la retroilluminazione. Anche nella seconda postazione ci sono 2 telecamere per avere un campo di lavoro molto più grande grazie a 2 ottiche. Oltre al sensore di visione IVG, vi sono quindi due controllori che governano in automatico le 4 telecamere e le 8 luci delle due postazioni. In particolare, un controllore gestisce una telecamera e il secondo controllore le altre 3 telecamere.
E’ stato possibile montare l’IVG in mezzo a due ottiche solo grazie alle sue dimensioni. Infatti, dovendo inquadrare la macchia di colore al centro del pezzo, le piccole dimensioni dell’IVG non disturbano il funzionamento delle due telecamere.
“Il successo della macchina, dovuto anche all’impiego del materiale Keyence, porterà presto a nuovi progetti. Ma di questo ne riparleremo”, conclude l’ingegner Fenoglio.
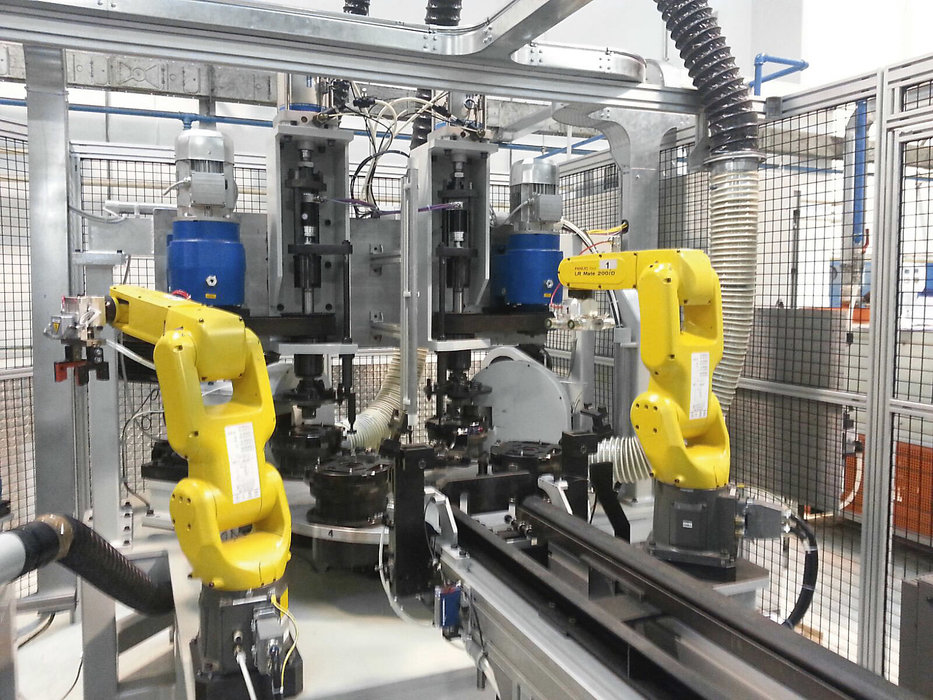
La macchina realizzata dal Gruppo Bonetto comprende due grosse mole e un sistema robotizzato che carica le ganasce da un alimentatore.
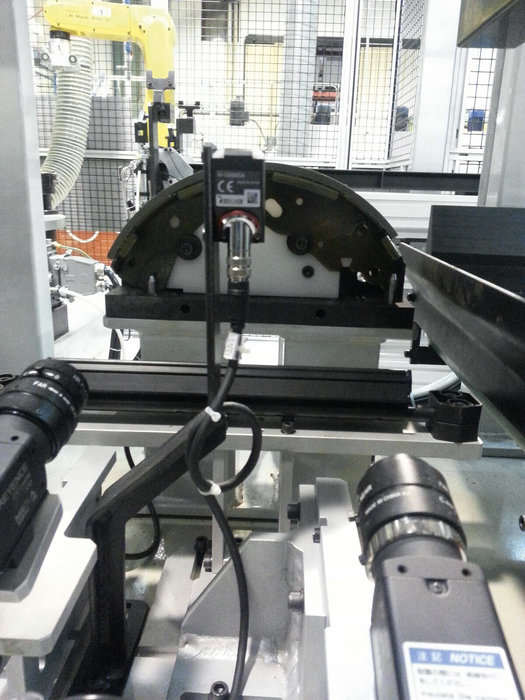
Due telecamere da 2MP Keyence, un sensore di visione IVG e due backlight permettono di verificare la presenza luce fascia/costa e il controllo presenza e colore marcatura.
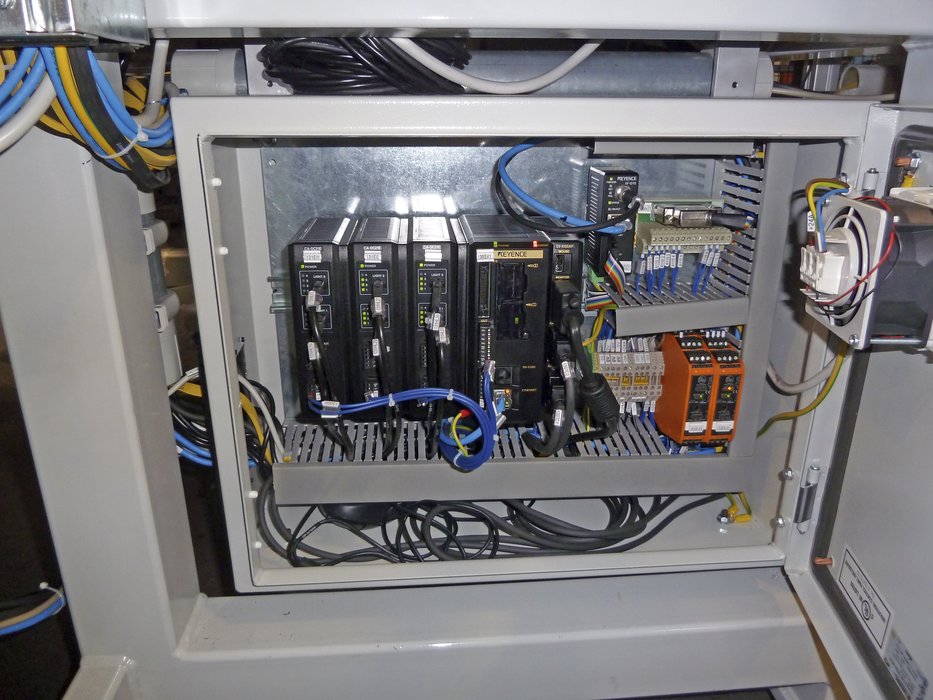
Due controllori Keyence governano in automatico le 4 telecamere e le 8 luci delle due postazioni.
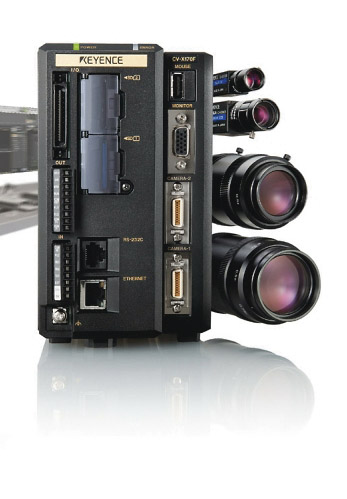
Richiedi maggiori informazioni…