www.industria-online.com
01
'20
Written on Modified on
Superare l'incertezza dei processi per ridurre scarti rilavorazioni
La qualità del prodotto rappresenta un indicatore chiave delle prestazioni per le imprese manufatturiere. Molte officine credono che ottenere le certificazioni di conformità agli standard qualitativi ISO, NADCAP e API garantisca la qualità del loro lavoro. In realtà, gli standard non si focalizzano su come produrre pezzi finiti accettabili, ma piuttosto su come stabilire procedure per rifiutare parti difettose
Si può avere un quadro veritiero della qualità del prodotto di un produttore guardando nell’area di controllo qualità dell’officina, specialmente dove ci sono parti con etichette o cartellini indicanti una “nuova ispezione”. Queste etichette indicano che per qualche ragione i pezzi sono stati rifiutati o devono tornare in produzione per essere rilavorati. Scarti e rilavorazioni si hanno quando il processo produttivo non soddisfa le aspettative. Alcuni processi, specialmente le lavorazioni meccaniche, sono basati sull’interazione di molte variabili e dunque sono soggetti ad incertezza e a un certo grado di inaffidabilità. È essenziale che i produttori riconoscano le fonti di incertezza, capiscano come si verificano e trovino un modo di risolverle. In molti casi, tuttavia, le fondi di incertezza nel processo non sono riconosciute o sono ignorate ed accettate come pratica standard. Alla fine, superare le incertezze e limitare scarti e rilavorazioni dipende in larga parte dalla coscienza, conoscenza e motivazione di chi lavora nell’officina.
Fonti di incertezza
La spinta della competizione porta i produttori a fare analisi di riduzione dei costi. Le analisi includono l’esame delle spese per i materiali, l’utensileria e il tempo di lavorazione. Cercare ed eliminare le varie perdite di tempo presenti offre possibilità significative di controllare i costi (vedi figura 1). I metodi utilizzati nelle analisi dei costi includono programmi OEE e Lean. Tali analisi, tuttavia, spesso si basano su una visione del processo di produzione come una sorta di scatola semplice e autonoma. Un’officina mette nella scatola materie prime o semilavorati, avvengono i processi di lavorazione, quindi un certo numero di pezzi esce dalla scatola, sia come prodotti finiti che come semilavorati destinati a un'altra scatola.
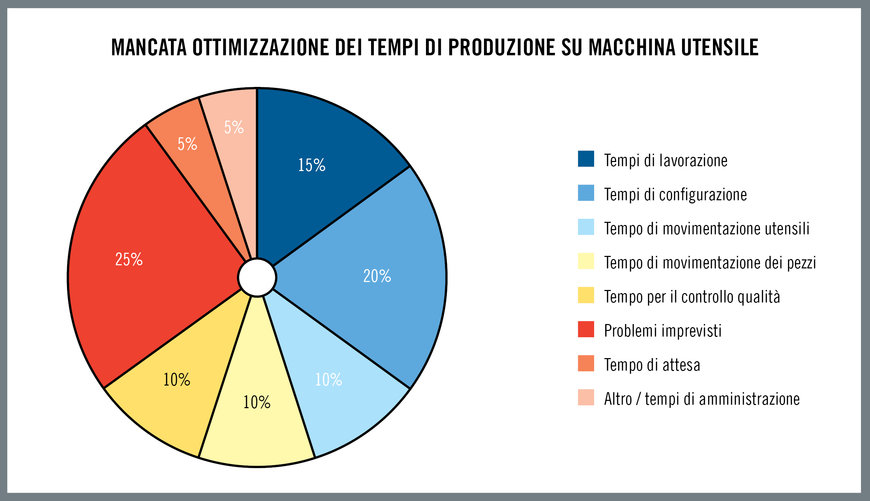
Figura 1:
Mancata ottimizzazione dei tempi di produzione su macchina utensile.jpg
Riconoscimento delle variabili di lavorazione
Ciò che spesso manca nelle analisi è il riconoscimento che nel mondo reale non è del tutto certo che ogni prodotto che esce dalla scatola sarà accettabile. I prodotti inaccettabili devono essere rilavorati o scartati completamente.
Il numero di pezzi prodotti inaccettabili dipende da quanto attentamente vengono controllate le variabili nel processo di fabbricazione. Processi come la forgiatura, ad esempio, non sono estremamente complessi e non richiedono un livello estremo di precisione. Questi processi sono quindi relativamente controllabili, affidabili e in grado di fornire costantemente il numero previsto di pezzi accettabili. Al contrario, altri processi produttivi coinvolgono più variabili che possono ridurre la prevedibilità del risultato. Il numero di pezzi accettabili che escono dalla scatola non è prevedibile in modo affidabile.
È un'esagerazione chiamare inaffidabili tutti i processi di lavorazione, ma è piuttosto accurato descriverli come non del tutto prevedibili. La lavorazione implica molte variabili. Essa sottopone gli utensili da taglio e i materiali del pezzo a forti forze di taglio ed alte temperature. La combinazione di forze e temperature crea una situazione complessa e dinamica. La durezza di un utensile determina la sua capacità di tagliare in maniera efficiente e la durezza varia tra la temperatura ambiente e le temperature di 800 ° C generate nella lavorazione. Il calore influisce anche sulle caratteristiche di lavorabilità del materiale del pezzo. Gli effetti delle variabili sono imprevedibili. Anche se vengono specificati i parametri di lavorazione per una determinata applicazione, i valori esatti in gioco durante il funzionamento saranno sconosciuti. Risultati diversi nella finitura superficiale o nelle dimensioni possono rendere una parte candidata per una rilavorazione o per essere scartata.
Quando le parti sono inaccettabili, è necessario esaminare due aree. Un'area è tecnologica: un produttore deve sapere cosa sta realmente accadendo, riconoscere quali variabili hanno causato il risultato imprevisto e decidere come risolvere il problema. L'altra area da esaminare riguarda la determinazione degli effetti finanziari della produzione di parti inaccettabili. Ciò include il calcolo del costo imprevisto del rifiuto o della rilavorazione e la decisione su come la società ne terrà conto.
Gli scenari di produzione di massa generalmente confrontano statisticamente il numero di parti inaccettabili con le centinaia o migliaia di parti prodotte nel complesso. Nei lunghi cicli di produzione, l’officina può analizzare l’operazione, notare i fattori che hanno prodotto le parti inaccettabili, e aggiornare i parametri di taglio per minimizzare l’incertezza e massimizzare l’affidabilità.
In scenari di produzione ad alto mix e basso volume, tuttavia, c'è un tempo minimo per esaminare parti inaccettabili e modificare i processi di lavorazione per eliminarle. La sfida è maggiore se un ciclo di produzione è costituito da un solo pezzo. Il problema si moltiplica ulteriormente quando l’officina non ha familiarità con il materiale del pezzo e il cliente finale richiede immediatamente il prodotto finito. Un risultato inaccettabile su un lavoro che coinvolge un solo pezzo richiede la lavorazione di un'altra parte, aumentando i costi e deludendo il cliente.
Nel caso della produzione di massa, eliminare la produzione di parti inaccettabili è relativamente semplice. Lo staff tecnologico esamina e aggiorna il processo, esegue prove e arriva a una soluzione. In scenari di produzione di massa reali, il numero di pezzi inaccettabili è relativamente molto piccolo rispetto alla produzione totale e i costi sono trascurabili. Ma nel caso di produzioni ad alto mix, a basso volume o anche a pezzo singolo, il costo di parti inaccettabili può ridurre gravemente i margini di profitto o addirittura provocare una perdita operativa. Il produttore ha solo un'opportunità per produrre un pezzo accettabile in un tempo estremamente limitato.
Costi nascosti o ignorati
Alcuni costi che dovrebbero essere inclusi nel costo totale di produzione potrebbero essere nascosti o ignorati. Un esempio è il costo della sbavatura. Un pezzo è considerato completo quando le sue finiture superficiali lavorate corrispondono alle specifiche e i suoi bordi e geometrie soddisfano i requisiti del progetto. Una parte con una bava non è completa. Sebbene una bava rappresenti una perdita nella qualità della lavorazione, esse sono spesso accettate come una normale conseguenza del processo. In ogni caso, le bave devono essere rimosse e il costo di questa operazione può essere significativo. In un esempio reale, un'officina altamente automatizzata con fresatrici a cinque assi ha prodotto una famiglia di parti che richiedevano la sbavatura manuale. Alla fine, il tempo e la manodopera coinvolti nella sbavatura rappresentavano il 20 percento del costo di un pezzo finito.
In alcuni casi, i calcoli di costo e prezzo per un pezzo si basano su processi di lavorazione senza considerare il costo della sbavatura o altre operazioni secondarie. Tali costi potrebbero non essere trascurabili. Per ottenere un quadro accurato del costo totale di produzione, i costi nascosti devono essere riconosciuti e ridotti.
Scelta dell’utensile
L'uso di attrezzature e utensileria adeguati minimizzerà la variabilità nelle operazioni. Le macchine utensili grandi e rigide possono resistere alle forze generate nelle lavorazioni pesanti, che causano errori dimensionali del pezzo. Alcune caratteristiche della macchina utensile, come le scale in vetro, le guide lineari e i sistemi di gestione termica, massimizzano la precisione.
La selezione degli utensili da taglio svolge un ruolo importante nel limitare la variabilità. Negli ultimi due o tre decenni, l'approccio alla scelta degli utensili si è evoluto. In precedenza, la scelta dell'utensile era sostanzialmente divisa tra utensili ad alte prestazioni, che offrivano le maggiori velocità di produzione possibili, e utensili economici che offrivano il minor costo possibile per parte. In alcuni casi, tuttavia, gli utensili più performanti erano relativamente fragili. Quando funzionavano bene, erano eccellenti, ma un'attenta applicazione era fondamentale. Gli utensili a basso costo non arrivavano alla velocità e alla capacità di output degli strumenti ad alte prestazioni, il vantaggio in termini di prezzo è a scapito di un output inferiore..
Quando si scelgono gli utensili oggi, una considerazione chiave prima di scegliere geometrie, velocità e avanzamento è ciò che un utente richiede in termini di prestazioni. Per operazioni di produzione di massa, rimane l'esigenza di utensili che massimizzino il tasso di asportazione e offrano la massima vita utensile possibile. Le applicazioni di altissima precisione richiedono utensili le cui dimensioni, caratteristiche di usura e parametri di applicazione sono stati sviluppati tenendo conto della massima accuratezza, sebbene questo porti a un costo premium dell'utensile.
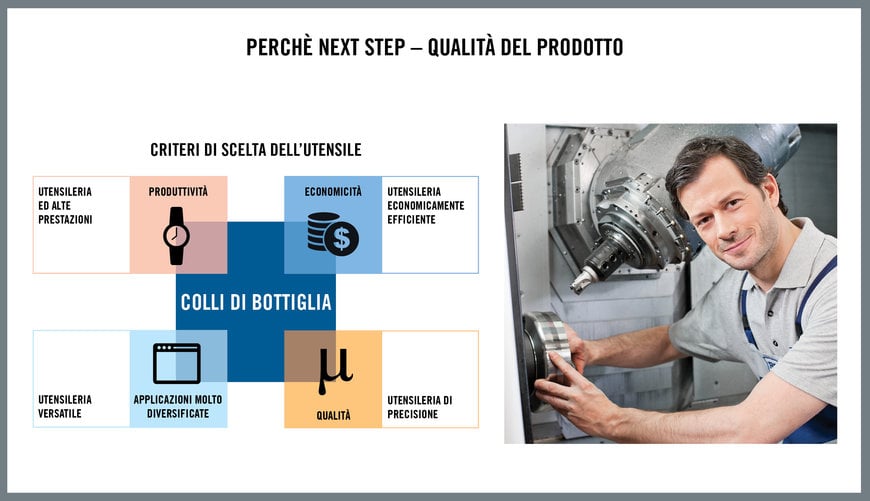
Figura 2:
Perchè Next Step – Qualità del prodotto.jpg
Nell'era attuale in cui gli scenari di produzione ad alto mix e basso volume sono frequenti, è estremamente importante che la qualità del pezzo finito soddisfi le aspettative la prima volta che il pezzo viene lavorato. L'attenzione si concentra su utensili che funzionano in un'ampia varietà di situazioni con tempi di sviluppo del processo minimi. Questo è il pensiero dietro lo sviluppo di utensili versatili (vedi barra laterale). Se utilizzato da ingegneri e operatori di produzione che conoscono le loro capacità e i loro limiti, gli utensili progettati per essere affidabili e versatili sono la risposta per molte applicazioni. Lavorare con un numero limitato di utensili versatili consente all'operatore di apprendere e comprendere le prestazioni degli utensili nel tempo, adattandosi alla lavorazione di vari pezzi diversi.
L’applicazione ragionata di un’utensileria versatile può minimizzare i pezzi respinti dal controllo qualità, e una maggiore sicurezza di processo può aiutare la gestione finanziaria ottenere un quadro preciso dei costi veri e margini di profitto.
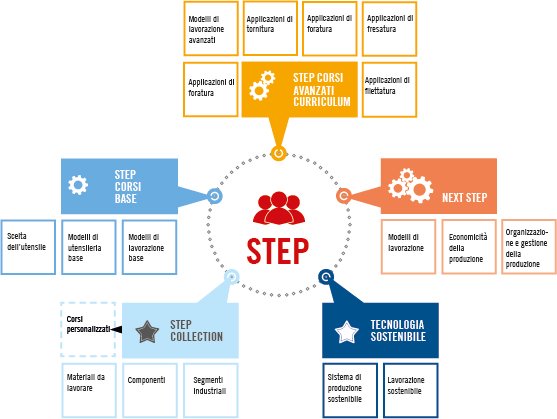
Figura 3:
STEP corso concetto grafico 2020.jpg
Contributi essenziali
L'incontro recente del mondo con il virus pandemico è servito a sottolineare il ruolo che le persone svolgono nel successo manifatturiero. Un’officina altamente automatizzata in Olanda è stata costretta a ridurre la produzione perché alcuni membri dello staff di erano malati a casa. Nonostante una grande presenza di robot, computer e intelligenza artificiale, quando le persone scompaiono, la produzione soffre. È chiaro che le persone rimangono l'elemento chiave della produttività. Una forza lavoro manifatturiera istruita, flessibile e motivata può adattarsi a scenari di produzione come situazioni ad alto mix e basso volume e fornire anche la risposta rapida necessaria per accelerare la produzione quando si verificano problemi imprevisti in un ambiente frenetico. Sono necessarie le capacità per utilizzare un computer, ma ugualmente o ancor più necessari sono avere un senso di come funziona il processo di lavorazione, un quadro di ciò che sono i risultati finali attesi e il desiderio di raggiungere tale obiettivo.
(Barra laterale)
Gli utensili versatili Seco soddisfano un'ampia gamma di esigenze
La maggior parte dei proprietari di officine di produzione ritiene che il loro compito sia acquistare "i migliori utensili disponibili". Ma rimanere senza risposta è la domanda "cosa ti aspetti dai tuoi utensili?" Per alcune officine, i tassi massimi di asportazione del metallo sono fondamentali, mentre altre richiedono una vita utensile lunga e costante per consentire un funzionamento realmente sicuro e affidabile.
"I migliori utensili qui sono…" è la frase che identifica gli utensili adatti alle parti, ai materiali dei pezzi, alle macchine utensili e ai programmi di produzione di una particolare officina. Dopo aver scelto gli utensili, può iniziare la discussione su qualità del metallo duro, geometrie, velocità e avanzamenti.
La scelta degli utensili richiede anche l'esame del contenuto e del flusso di lavoro complessivo di un'organizzazione. In un recente esempio, un proprietario di un'officina meccanica si è reso conto che stava spendendo € 200.000-250.000 all'anno in utensileria. Un controllo alle scorte di utensili presso la sua azienda ha rivelato circa € 700.000 di inventario. Si è scoperto che l’officina produceva generalmente piccoli lotti di pezzi e ogni volta che c’era un nuovo tipo di pezzo o materiale nuovo, il proprietario dell’officina aggiungeva quello che pensava fosse l’utensile migliore e più performante per il lavoro. Di conseguenza, l’officina ha accumulato un ampio inventario dei migliori utensili possibili che nessuno sapeva davvero come utilizzare, nonché utensili inutilizzabili Poiché acquistati per un lavoro unico che non si è mai ripetuto.
Per evitare situazioni simili, Seco offre la propria selezione di utensili versatili. Gli utensili non offrono necessariamente le massime prestazioni possibili, ma sono affidabili, facili da usare e progettati per essere applicati in modo molto produttivo su una vasta gamma di materiali e geometrie dei pezzi. Un utensile versatile può essere utilizzato un giorno su acciaio, il giorno successivo su acciaio inossidabile, il giorno dopo su alluminio e alla fine della settimana su titanio. Non sono utensili di seconda scelta, ma piuttosto la prima scelta per l'equilibrio tra prestazioni e flessibilità necessarie per elaborare in modo efficiente i progetti di lavorazione ad alto mix e basso volume caratteristici della produzione odierna. Con un utensile versatile, un operatore esperto può compiere miracoli economici e produttivi.
Richiedi maggiori informazioni…