www.industria-online.com
12
'09
Written on Modified on
Il mercato dell'aeronautica chiede più connettori modulari ad alta densità
Per ridurre il peso e ottimizzare l'elaborazione delle informazioni, l'architettura dei calcolatori elettronici di bordo si è evoluta da semplici unità di controllo dedicate ad una singola funzione (integrazione di segnali provenienti da sensori, fusione di dati, image processing, etc) a unità di controllo multifunzionali. Tale evoluzione ha inevitabilmente reso necessario anche un progressivo adattamento dei connettori.
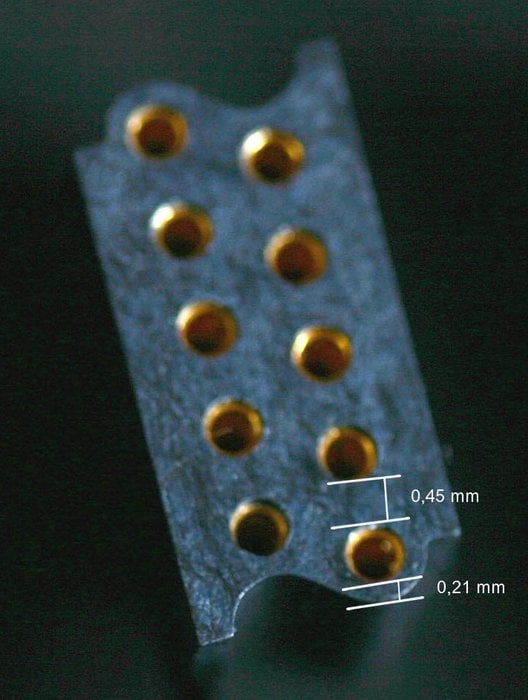
Ridurre il peso dei velivoli è essenziale per conferire maggiore potenza in fase di decollo e aumentare l'efficienza del carburante utilizzato. Ciò è molto importante in termini di costi, ma anche per affrontare le distanze geografiche crescenti che i futuri aeromobili dovranno coprire. E utilizzare nuovi materiali in fase di costruzione non è l'unico modo per ottenere questa riduzione di peso. Ridurre il numero dei componenti semplificando la struttura e la composizione dei sistemi elettronici a bordo degli aerei è un altro approccio molto efficace. Tra l'altro, con questo approccio non si riduce soltanto il peso degli aeromobili: strutture più compatte permettono un processo di assemblaggio e delle operazioni di manutenzione più semplici.
Una delle maggiori tendenze del momento nel settore aeronautico è quella di ridurre il peso attraverso una riduzione del numero delle unità di controllo a bordo. Ciò richiede la progettazione di unità di elaborazione capaci di eseguire fino a quattro task in real-time, con la conseguente necessità di gestire segnali misti (digitali, analogici, di potenza, d’alta frequenza, Ethernet, e così via) e di inviarli da una scheda elettronica all'altra. Tale necessità ha portato a gestire un’ampiezza di banda sempre maggiore, fino agli attuali 10 Gb/s. A questo trend si è aggiunta poi la preferenza per l'impiego a bordo di connessioni in fibra ottica, sempre più apprezzate in virtù del loro peso leggero e dell'elevata capacità trasmissiva. Questa preferenza per la fibra ottica ha progressivamente coinvolto diversi tipi di connessione (connettori multipli, cablaggio extra, ecc.), aumentando però i rischi di errori trasmissivi, la complessità dell'installazione e il peso di cablaggio extra a bordo degli aerei. Poter sviluppare sul mercato un nuovo connettore in grado di gestire in modo migliore questo tipo di segnali misti è stata una sfida importante per i produttori sul mercato.
Il requisito principale di un nuovo connettore capace di vincere questa sfida deve consistere nella capacità di riunire la maggior parte di queste connessioni in un singolo dispositivo, in un'unità molto compatta. Dato che sarebbe troppo costoso personalizzare un connettore per ogni esigenza specifica del cliente, la struttura del connettore deve essere necessariamente modulare. Un connettore ad alta densità deve essere composto da diversi moduli che possono essere liberamente assemblati. I moduli possono essere integrati con i tradizionali contatti di segnale elettrico, coassiale, fibra ottica o di potenza in base ai requisiti di progettazione iniziale. Questo approccio induce però a ripensare i limiti meccanici tradizionali dei set di contatti isolati del connettore. Il principio dei moduli impilabili dimezza lo spessore delle pareti laterali tra i contatti presa esterni (si veda la Figura 1): da 0,45 mm a 0,21 mm.
Per vincere questa sfida, Amphenol-Socapex ha sviluppato un nuovo connettore chiamato HILINX. Esso si basa su un particolare layout ad 'S' che fa sì che i moduli del connettore siano impilabili senza perdere i contatti tra un modulo e l'altro (viene cioè garantita la continuità spaziale tra i contatti). Le unità sono mantenute in sede da due gusci in acciaio inossidabile, uno su ogni lato.
Ciò ha reso necessario aggiungere al connettore uno strato isolante plastico molto sottile, capace di conferire al connettore una resistenza alle condizioni ostili tipiche degli ambienti militari ed aeronautici (vibrazioni, shock termici ecc). Lo strato isolante deve essere privo dei difetti tipici dei materiali plastici (ad esempio, quelle difettosità legate alla fase di stampaggio della plastica), in modo da fornire adeguata resistenza meccanica e protezione da archi elettrici (rigidità dielettrica paria a 750 VRms a 60 Hz, in conformità allo standard MIL-DTL-55302).
Le tolleranze in fase di produzione, allo stesso modo, sono state mantenute sempre molto ridotte e, per evitare tutti i rischi di inquinamento, non è stato utilizzato alcun lubrificante per inserire i componenti. I contatti sono dunque tutti realizzati nel diametro richiesto dal cliente senza ri-lavorazioni, in un range di tolleranza di 0.03.
È stato dunque progettato un nuovo connettore con tolleranze meccaniche minime. Il ciclo termico è ottimizzato in 'closed loop' per fornire eccellenti livelli di performance in fase di stampaggio della plastica con un'elevata precisione dimensionale (per la plastica realizzata con stampi ad iniezione) e un'eccellente trattamento della superficie. Gli inserti in plastica forniscono livelli di tolleranza dimensionale di circa 0.05 mm. I gusci che tengono insieme i moduli e forniscono la continuità dei contatti tra un modulo e l’altro presentano invece una tolleranza di 0.03 mm.
Il meccanismo di fissaggio e antiscivolamento permette un perfetto posizionamento del modulo: per ottenere questo risultato è stato necessario un lungo percorso di ottimizzazione del fissaggio. L’intero processo di produzione è sottoposto a verifica a campione.
I gusci sono saldati ai moduli pre-assemblati utilizzando un biadesivo che non si deforma né si espande in presenza di calore, è resistente all'umidità e risponde perfettamente ai requisiti del settore aeronautico.
Il materiale di isolamento utilizzato è una resina termoplastica LCP (Liquid Crystal Polymer), che presenta un’ottima rigidità dielettrica, una migliore resistenza al calore e agli agenti chimici, un’eccellente stabilità dimensionale e, in più, presenta livelli di infiammabilità e di assorbimento dell’umidità molto bassi.
La particolare tecnica di costruzione a moduli impilabili senza perdita di contatti tra un modulo e l’altro assicura una perfetta continuità nell’allineamento dei contatti. Ciò significa che questo nuovo connettore è compatibile al 100% (solo nella versione di contatto di segnale) con i più noti connettori standard monoblocco del mercato aeronautico (M55302/190 fino a /193).
Il passo tra i contatti di segnale è di 1.905 mm, con una disposizione a file alterne. I moduli possono essere composti da 2, 3, 4 o 6 file. I contatti di segnale seguono il principio ‘Starclip’, che fornisce caratteristiche uniche in termini di affidabilità ed è testato secondo lo standard MIL DTL 55302, dopo aver superato le più severe prove, inclusi il test di resistenza alle vibrazioni e agli urti (con il monitoraggio della continuità elettrica a 2 ns in modalità dinamica durante tutti i test eseguiti).
Amphenol fornisce la più ampia gamma di contatti disponibile sul mercato: rame (segnali, potenza, HF, Quadrax ecc) e fibra ottica (giunzione di testa, lenti ecc). Ad esempio, possono essere disponibili connessioni ibride per contatti di potenza RADSOK¬Æ. I contatti maschio con diametro di 2.4 mm possono condurre correnti fino a 35A pur occupando pochissimo spazio in moduli con tre file di contatti di segnale.
I connettori sono progettati per ambienti ostili: il range di temperatura ammissibile varia da -65 °C a +150 °C e il tempo di resistenza agli spruzzi salini è pari a 96 ore. I connettori sono resistenti agli urti e alle vibrazioni, sia in conformità con i test previsti dalle normative SAE AS 13441 (secondo le modalità del 2004 e del 2005), sia ad altri campi di vibrazione più specifici per alcuni programmi aeronautici. La resistenza massima dei contatti di segnale è pari a 10 mohm.
Le applicazioni tipiche del nuovo connettore Amphenol riguardano soprattutto il settore aeronautico, ma il connettore può trovare impiego anche nel settore medicale, nei controllori automatici nel campo dell’automazione, nel settore ferroviario e petrolifero, e nelle applicazioni militari. Il connettore HILINX agevola le procedure di progettazione e realizzazione delle connessioni su circuito stampato e riduce il numero di componenti, presentando i massimi livelli di performance e affidabilità. HILINX rappresenta una soluzione di connessione molto compatta e poco costosa.
Figura 2, 3 e 4: esempi di trasmissione di segnali misti nello stesso connettore.
Una delle maggiori tendenze del momento nel settore aeronautico è quella di ridurre il peso attraverso una riduzione del numero delle unità di controllo a bordo. Ciò richiede la progettazione di unità di elaborazione capaci di eseguire fino a quattro task in real-time, con la conseguente necessità di gestire segnali misti (digitali, analogici, di potenza, d’alta frequenza, Ethernet, e così via) e di inviarli da una scheda elettronica all'altra. Tale necessità ha portato a gestire un’ampiezza di banda sempre maggiore, fino agli attuali 10 Gb/s. A questo trend si è aggiunta poi la preferenza per l'impiego a bordo di connessioni in fibra ottica, sempre più apprezzate in virtù del loro peso leggero e dell'elevata capacità trasmissiva. Questa preferenza per la fibra ottica ha progressivamente coinvolto diversi tipi di connessione (connettori multipli, cablaggio extra, ecc.), aumentando però i rischi di errori trasmissivi, la complessità dell'installazione e il peso di cablaggio extra a bordo degli aerei. Poter sviluppare sul mercato un nuovo connettore in grado di gestire in modo migliore questo tipo di segnali misti è stata una sfida importante per i produttori sul mercato.
Il requisito principale di un nuovo connettore capace di vincere questa sfida deve consistere nella capacità di riunire la maggior parte di queste connessioni in un singolo dispositivo, in un'unità molto compatta. Dato che sarebbe troppo costoso personalizzare un connettore per ogni esigenza specifica del cliente, la struttura del connettore deve essere necessariamente modulare. Un connettore ad alta densità deve essere composto da diversi moduli che possono essere liberamente assemblati. I moduli possono essere integrati con i tradizionali contatti di segnale elettrico, coassiale, fibra ottica o di potenza in base ai requisiti di progettazione iniziale. Questo approccio induce però a ripensare i limiti meccanici tradizionali dei set di contatti isolati del connettore. Il principio dei moduli impilabili dimezza lo spessore delle pareti laterali tra i contatti presa esterni (si veda la Figura 1): da 0,45 mm a 0,21 mm.
Per vincere questa sfida, Amphenol-Socapex ha sviluppato un nuovo connettore chiamato HILINX. Esso si basa su un particolare layout ad 'S' che fa sì che i moduli del connettore siano impilabili senza perdere i contatti tra un modulo e l'altro (viene cioè garantita la continuità spaziale tra i contatti). Le unità sono mantenute in sede da due gusci in acciaio inossidabile, uno su ogni lato.
Ciò ha reso necessario aggiungere al connettore uno strato isolante plastico molto sottile, capace di conferire al connettore una resistenza alle condizioni ostili tipiche degli ambienti militari ed aeronautici (vibrazioni, shock termici ecc). Lo strato isolante deve essere privo dei difetti tipici dei materiali plastici (ad esempio, quelle difettosità legate alla fase di stampaggio della plastica), in modo da fornire adeguata resistenza meccanica e protezione da archi elettrici (rigidità dielettrica paria a 750 VRms a 60 Hz, in conformità allo standard MIL-DTL-55302).
Le tolleranze in fase di produzione, allo stesso modo, sono state mantenute sempre molto ridotte e, per evitare tutti i rischi di inquinamento, non è stato utilizzato alcun lubrificante per inserire i componenti. I contatti sono dunque tutti realizzati nel diametro richiesto dal cliente senza ri-lavorazioni, in un range di tolleranza di 0.03.
È stato dunque progettato un nuovo connettore con tolleranze meccaniche minime. Il ciclo termico è ottimizzato in 'closed loop' per fornire eccellenti livelli di performance in fase di stampaggio della plastica con un'elevata precisione dimensionale (per la plastica realizzata con stampi ad iniezione) e un'eccellente trattamento della superficie. Gli inserti in plastica forniscono livelli di tolleranza dimensionale di circa 0.05 mm. I gusci che tengono insieme i moduli e forniscono la continuità dei contatti tra un modulo e l’altro presentano invece una tolleranza di 0.03 mm.
Il meccanismo di fissaggio e antiscivolamento permette un perfetto posizionamento del modulo: per ottenere questo risultato è stato necessario un lungo percorso di ottimizzazione del fissaggio. L’intero processo di produzione è sottoposto a verifica a campione.
I gusci sono saldati ai moduli pre-assemblati utilizzando un biadesivo che non si deforma né si espande in presenza di calore, è resistente all'umidità e risponde perfettamente ai requisiti del settore aeronautico.
Il materiale di isolamento utilizzato è una resina termoplastica LCP (Liquid Crystal Polymer), che presenta un’ottima rigidità dielettrica, una migliore resistenza al calore e agli agenti chimici, un’eccellente stabilità dimensionale e, in più, presenta livelli di infiammabilità e di assorbimento dell’umidità molto bassi.
La particolare tecnica di costruzione a moduli impilabili senza perdita di contatti tra un modulo e l’altro assicura una perfetta continuità nell’allineamento dei contatti. Ciò significa che questo nuovo connettore è compatibile al 100% (solo nella versione di contatto di segnale) con i più noti connettori standard monoblocco del mercato aeronautico (M55302/190 fino a /193).
Il passo tra i contatti di segnale è di 1.905 mm, con una disposizione a file alterne. I moduli possono essere composti da 2, 3, 4 o 6 file. I contatti di segnale seguono il principio ‘Starclip’, che fornisce caratteristiche uniche in termini di affidabilità ed è testato secondo lo standard MIL DTL 55302, dopo aver superato le più severe prove, inclusi il test di resistenza alle vibrazioni e agli urti (con il monitoraggio della continuità elettrica a 2 ns in modalità dinamica durante tutti i test eseguiti).
Amphenol fornisce la più ampia gamma di contatti disponibile sul mercato: rame (segnali, potenza, HF, Quadrax ecc) e fibra ottica (giunzione di testa, lenti ecc). Ad esempio, possono essere disponibili connessioni ibride per contatti di potenza RADSOK¬Æ. I contatti maschio con diametro di 2.4 mm possono condurre correnti fino a 35A pur occupando pochissimo spazio in moduli con tre file di contatti di segnale.
I connettori sono progettati per ambienti ostili: il range di temperatura ammissibile varia da -65 °C a +150 °C e il tempo di resistenza agli spruzzi salini è pari a 96 ore. I connettori sono resistenti agli urti e alle vibrazioni, sia in conformità con i test previsti dalle normative SAE AS 13441 (secondo le modalità del 2004 e del 2005), sia ad altri campi di vibrazione più specifici per alcuni programmi aeronautici. La resistenza massima dei contatti di segnale è pari a 10 mohm.
Le applicazioni tipiche del nuovo connettore Amphenol riguardano soprattutto il settore aeronautico, ma il connettore può trovare impiego anche nel settore medicale, nei controllori automatici nel campo dell’automazione, nel settore ferroviario e petrolifero, e nelle applicazioni militari. Il connettore HILINX agevola le procedure di progettazione e realizzazione delle connessioni su circuito stampato e riduce il numero di componenti, presentando i massimi livelli di performance e affidabilità. HILINX rappresenta una soluzione di connessione molto compatta e poco costosa.
Figura 2, 3 e 4: esempi di trasmissione di segnali misti nello stesso connettore.
Richiedi maggiori informazioni…