www.industria-online.com
18
'11
Written on Modified on
Produzione di contenitori in vetro per uso farmaceutico
S.P.A.M.I., un’azienda che fa parte dello Stevanato Group, ha sviluppato un sistema di ispezione per migliorare la qualità delle parti in vetro. Esso utilizza tecnologie di controllo della qualità per vagliare i tubi di vetro che arrivano allo stabilimento e anche il prodotto finale. Il sistema include un sistema di ispezione visiva (NoVIS), un sistema per la misura continua della temperature anche un sistema di elaborazione digitale delle immagini, denominato CLEANER, che è in grado di rilevare e rimuovere difetti nel vetro fino alle dimensioni di pochi micron nel prodotto finale. Il macchinario di processo, completamente integrato, misura il diametro del tubo di vetro, lo spessore delle pareti e la temperatura mediante pirometri a infrarossi (controllo di ricottura con pirometro) per il controllo totale della qualità, mentre bruciatori motorizzati offrono uno stretto controllo del loro posizionamento. L’uso di questo sistema assicura a Stevanato un vantaggio di qualità rispetto ad altri produttori di fiale. Per questo sistema avanzato, S.P.A.M.I. utilizza convertitori Anybus HMS per il collegamento fra le telecamere di ispezione visiva remote e i PLC che controllano le linee di produzione.
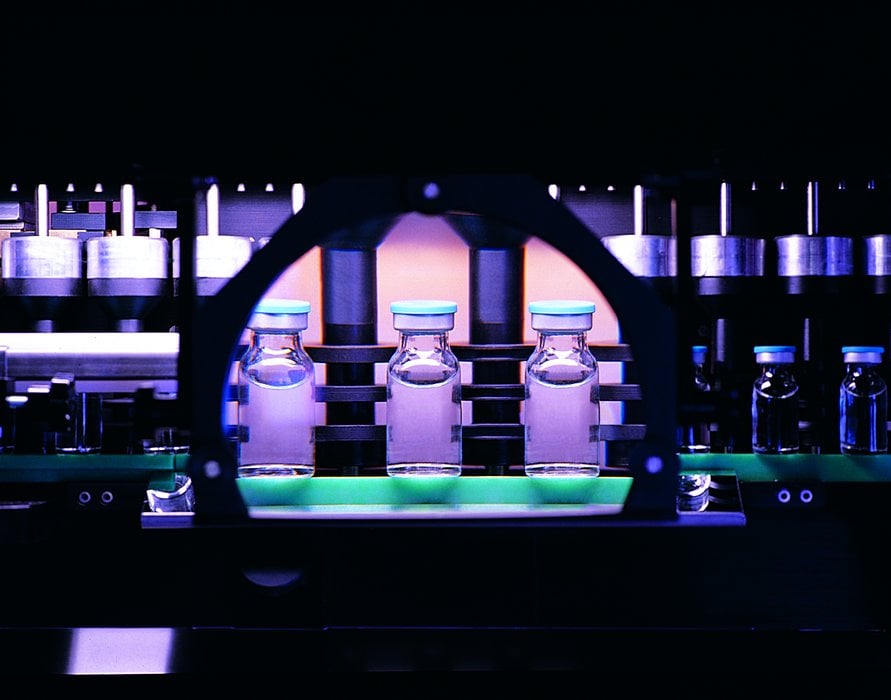
Il gruppo comprende due divisioni. La Divisione Vetro, in particolare, è specializzata nella produzione di confezioni primarie in tubo di vetro per uso farmaceutico. Essa offre un’ampia gamma di prodotti, dalle confezioni primarie più tradizionali, come ampolle e fiale, a prodotti in rapida crescita come cartucce per autoiniettori e sistemi di iniezione a penna, incluse le siringhe sterili pronte all’uso.
La Divisione Ingegneria, formata dalle aziende S.P.A.M.I. e Optrel, è focalizzata sulla progettazione e produzione di macchinari ed apparecchiature per la conversione, l’ispezione visiva e il monitoraggio dei contenitori in tubo di vetro. La sinergia fra le due divisioni permette a Stevanato Group il pieno controllo sull’intero processo di produzione, dall’acquisto delle materie prime fino al supporto postvendita.
»La produzione di S.P.A.M.I. è destinata sia alle imprese interne al gruppo, sia alla vendita ad altre aziende esterne». Le soluzioni meccaniche ed elettriche installate sulle macchine formatrici sono state progettate in modo da offrire la massima precisione e i migliori risultati nella produzione di contenitori di vetro.
Tutti i componenti usati per formare il vetro fuso sono installati e attentamente verificati per garantire la tolleranza dimensionale di fiale, siringhe, cartucce ed ampolle. I componenti installati nelle macchine formatrici e sui nastri trasportatori sono stati specificamente selezionati in modo da evitare la contaminazione dei contenitori. Il processo è completamente automatico, dal caricamento del tubo all’inscatolamento. Il ciclo di produzione inizia dal tubo di vetro, che viene acquistato esternamente in parti aventi una lunghezza di circa 1,5 m e un diametro appropriato per le dimensioni del prodotto finito. Il tubo di vetro è introdotto in macchine formatrici rotanti con numerose teste di processo ed è riscaldato mediante bruciatori. In base al ciclo di processo, che è selezionato in funzione del prodotto da realizzare, vengono formati in questo modo la bocca e il fondo della fiala, ampolla, siringa, ecc..
Sulla linea sono installate le seguenti apparecchiature:
A valle delle macchine formatrici vi è un nastro trasportatore, dove sono eseguite ispezioni dimensionali e cosmetiche per mezzo di telecamere, per assicurare un controllo approfondito dei contenitori di vetro. »Si tratta fondamentalmente di misure dimensionali eseguite analizzando l’immagine», ha spiegato Gobita. »Poiché il prodotto è soggetto a stress meccanico durante il processo, vi è anche un forno di ricottura che fornisce un ciclo di riscaldamento per eliminare la tensione che si forma nel vetro». La fase finale comprende quindi il controllo di qualità del prodotto finito e l’imballaggio automatico. Si può notare che la parte finale del ciclo viene eseguita in modo tale da assicurare i livelli di qualità e sterilità richiesti per l’uso in applicazioni farmaceutiche.
Sul mercato vi è una serie di concorrenti che operano a livello internazionale. »I nostri principali concorrenti sono tedeschi e americani, mentre le altre aziende in Italia sono molto più piccole di noi», ha spiegato Gobita.
Il valore aggiunto offerto da S.P.A.M.I. è da cercarsi soprattutto nella qualità dei suoi prodotti, che le ha permesso di eccellere in questo settore.» Essendo utilizzati in applicazioni farmaceutiche, i nostri prodotti hanno requisiti di qualità molto elevati e devono rispondere a limiti normativi molto stringenti. Ciò richiede una grande quantità di personale di Controllo Qualità molto qualificato», ha proseguito Gobita. »La differenza fra noi e i nostri concorrenti nazionali può essere vista in questo aspetto particolare. Anche la nostra capacità di ricerca e sviluppo è un fattore importante: quando le aziende farmaceutiche ci chiedono prodotti di prova che sono diversi dai prodotti standard, possiamo progettare tali prodotti perché siamo in grado di modificare i nostri sistemi. Come divisione meccanica che produce i sistemi all’interno del gruppo, S.P.A.M.I. può modificare e adattare tali sistemi per rispondere ai requisiti di produzione. Questa capacità di customizzare i sistemi è un altro importante valore aggiunto che possiamo offrire ai nostri clienti. E’ necessario ricordare che nel settore farmaceutico vi sono molti prodotti standard, come ampolle e fiale, che tutti conosciamo, ma vi sono anche molti prodotti speciali – e la loro quantità sta crescendo – che per la maggior parte sono sviluppati ad hoc. In questi casi, è necessaria una macchina specifica, quindi nella maggioranza dei casi è necessario modificare una macchina preesistente».
Una collaborazione positiva con HMS
L’associazione con HMS è nata per risolvere uno specifico problema di comunicazione.
La divisione meccanica ha sviluppato un’applicazione per eseguire una serie di controlli di qualità sui prodotti basati sulla tecnologia della visione artificiale. Più nello specifico, era necessario collegare telecamere intelligenti Cognex a PLC Siemens. »Dovevamo quindi dotare le telecamere di interfaccia Ethernet per potere comunicare con i PLC mediante protocollo Profibus», ha spiegato Gobita. »Dopo un’attenta ricerca, e tramite EFA Automation, i distributori esclusivi in Italia delle soluzioni GATEWAY di HMS, abbiamo selezionato i dispositivi Anybus che ci hanno permesso di risolvere il problema della comunicazione fra le nostre apparecchiature».
All’epoca sono stati considerati anche altri potenziali fornitori, ma HMS era l’unica azienda che potesse offrire un’ampia gamma di convertitori di protocollo. »Questa capacità diffusa è stata centrale per la nostra scelta, perché le nostre varie applicazioni sono spesso molto diverse tra loro. Inizialmente, per esempio, avevamo la necessità di gestire il protocollo Profibus, che era utilizzato dai PLC Siemens, ma la nostra azienda usa normalmente anche controllori programmabili di altri fornitori. Per noi è quindi essenziale avere una gamma di prodotti estesa». Il primo prodotto HMS utilizzato era un dispositivo della famiglia di convertitori Anybus che converte da Profibus a Modbus su Ethernet: l’Anybus X-gateway.
Su ogni linea di produzione potrebbe essere installato più di un convertitore Anybus. »Finora, abbiamo usato una serie di convertitori, perché l’applicazione è stata usata in vari sistemi», ha proseguito Gobita. »Per controllare vari aspetti di qualità dei prodotti vengono utilizzate smart camera, che devono essere installate in più punti differenti del sistema. Fondamentalmente, questa non è un’applicazione ‘una tantum’ dei convertitori HMS, ma un’applicazione che per noi è diventata standard». »Siamo molto soddisfatti della nostra scelta. I prodotti Anybus di HMS sono molto solidi, funzionali e semplici da usare rispetto ad altri dispositivi simili che abbiamo provato. Tutti sappiamo che è molto facile trovare cose complesse, ma non è così facile trovare cose semplici.
Non abbiamo avuto alcun problema e da ciò è dipeso anche il modo con il quale si sono sviluppate le cose. In futuro, prevediamo di usare i convertitori Anybus HMS anche su altre linee, dove essi saranno naturalmente strettamente collegati ai nostri sistemi di controllo tramite telecamere. E, poiché gli standard richiedono tolleranze sempre più strette, è inevitabile che i controlli mediante telecamere remote aumenteranno», ha concluso Gobita.
Richiedi maggiori informazioni…