www.industria-online.com
21
'10
Written on Modified on
Genzyme monitorizza 50.000 punti SCADA con Anybus Communicator
L’azienda, leader mondiale nella biotecnologia, sta creando un nuovo sito di produzione di anticorpi policlonali. Si tratta di uno stabilimento innovativo: il processo è stato automatizzato il più possibile, per ridurre l’errore umano nelle numerose fasi del processo (separazione, purificazione, filtraggio, ultrafiltraggio, emoassorbimento, ecc.). Ciò implica la capacità di interfacciamento con una batteria di apparecchiature di laboratorio molto eterogenee, che non erano state inizialmente progettate per comunicare con fieldbus. Genzyme ha utilizzato circa trenta gateway Anybus Communicator HMS, per consentire la gestione SCADA coerente di tutti i dispositivi in uso. Vi sono stati benefici tanto in termini di qualità quanto in costi di produzione.
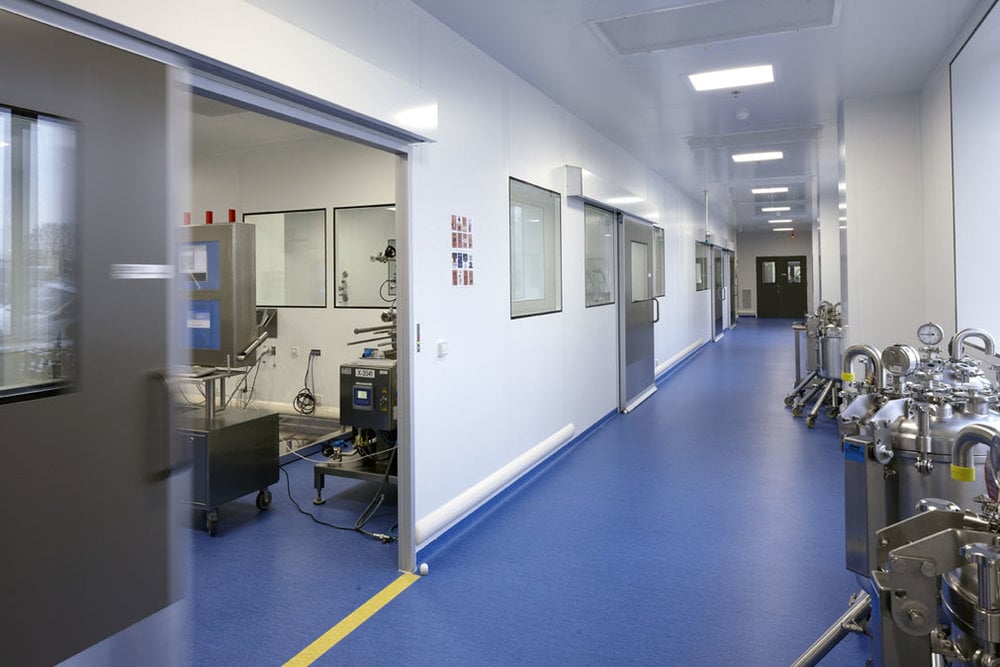
Il sito di bioproduzione di Lione si estende su un’area di 22,000 m², e produce un immunosoppressore selettivo che è usato per prevenire e trattare il rigetto degli organi durante i trapianti di organi (Thymoglobulin®).Questo farmaco è usato anche in ematologia nei casi in cui le celle trapiantate reagiscono contro il loro ospite nei trapianti di midollo osseo. Gli agenti attivi in questo farmaco sono immunoglobuline di timociti antiumani, ottenute dalla purificazione di un siero che è utilizzato come materia prima. La base immunogenica consiste di timociti (celle di Thymus), una sorgente naturale di celle T. Lo sviluppo di questo sito ha richiesto un investimento di 115 milioni di euro.
“Nel sito Sanofi Pasteur di Marcy, Genzyme sta attualmente utilizzando metodi di produzione a elevato contenuto di manodopera. Con questo nuovo sito, ci auguriamo di ottimizzare il processo in modo da ridurre l’errore umano al minimo assoluto. Questo processo a lotti altamente sequenziale implica oltre 780 fasi di produzione. Vi sono quindi numerose sorgenti di errore. Automatizzare un processo come questo ha richiesto molto stretto lavoro con le apparecchiature coinvolte per decidere come il sistema doveva comportarsi. Ciò ha evitato la necessità di ripensare l’intera ergonomia dell’edificio e delle apparecchiature di produzione, pur traducendosi in una vera rivoluzione nel modo in cui il processo di produzione funziona. Per ottenere tale risultato, abbiamo specificato oltre 4.000 parametri e 13.000 allarmi, che ci hanno permesso di governate ogni fase della produzione”, spiega Alexis Ducancel, responsabile Sistemi Automatizzati di Genzyme.
Bioproduzione: una serie di processi complessi
A differenza della chimica tradizionale, la produzione basata su cellule vive implica molte fasi differenti complesse e costose. Il ciclo di produzione di una proteina ricombinante richiede un’infrastruttura industriale adatta per la produzione a larga scala, che implica numerose fasi scaglionate su diversi mesi. Ogni fase è soggetta a numerosi controlli di qualità. Durante l’intero ciclo di produzione vengono effettuati test per assicurare l’assenza di virus e contaminanti. Alla fine della linea, si controllano anche la purezza e l’azione della proteina.
La produzione di questo farmaco implica molte fasi complesse, punteggiate da una successione di test tecnici e di verifica della qualità. Il processo di produzione può essere suddiviso in quattro fasi principali:
- La raccolta delle immunoglobuline, che avviene iniettando tessuto umano in conigli.
- La purificazione delle immunoglobuline per rimuovere proteine indesiderate (soprattutto anticorpi antieritrociti), tramite emoassorbimento.
- La fase di cromatografia consiste nello scambio anionico tramite l’uso di una resina di scambio ionico. Le impurità sono catturate dalla resina, mentre le immunoglobuline, che non hanno carica negativa, sono eluite. Questa fase è verificata mediante spettrofotometria ed elettroforesi.
- La fase di precipitazione serve per eliminare le ultime impurità rimanenti. Le immunoglobuline purificate sono pastorizzate (a 60°C per 10 ore).Questa soluzione è essiccata tramite raffreddamento prima di essere sigillata in fiale.
“In questo processo possiamo, ad esempio, programmare le impostazioni delle centrifughe (velocità, temperatura, tempo di funzionamento, ecc.). Questi valori possono essere modificati nello SCADA per tenere conto delle specifiche esigenze dell’attuale lotto di produzione. Le letture vengono effettuate in ogni fase e ritrasmesse allo SCADA. Questo ci permette di mettere in atto un processo di tracciabilità molto preciso. In particolare, ciò significa che il carico di lavoro per i team di verifica della qualità è significativamente ridotto, con un conseguente vantaggio in termini di costi”, aggiunge Alexis Ducancel.
Il sito di Lione, come quello di Marcy, riceverà le omologazioni FDA e AFFAPS.
“Naturalmente, abbiamo scelto HMS perché sentivamo che nessun’altra azienda aveva soluzioni standard a disposizione per restituire dati da un set di apparecchiature molto eterogenee, che non sono state necessariamente progettate per il collegamento a fieldbus. Abbiamo 28 centrifughe, pH-metri, bilance e così via. I protocolli d’interfaccia variano: seriale o ASCII, per esempio. I 30 Anybus Communicator sul posto ritrasmettono i dati su Ethernet o Profibus allo SCADA centrale”.
Anybus Communicator: la soluzione per integrare apparecchiature seriali in una rete di comunicazione industriale
La serie di gateway Anybus Communicator per il collegamento a Ethernet industriale/Fieldbus permette di collegare in rete dispositivi che sono stati sviluppati per l’uso in una rete seriale. L’Anybus Communicator può collegare la maggior parte dei prodotti con interfaccia seriale RS-232/422/485 a un’Ethernet industriale o un fieldbus. Esso esegue una conversione intelligente fra il protocollo seriale e la rete di destinazione. Tale conversione è configurata usando il software “ABC Config Tool”. La configurazione di rete, una volta completata, può essere riutilizzata per tutte le reti supportate dal Communicator.
“A parte la qualità del prodotto, abbiamo scoperto che il supporto tecnico era presente ogni volta che ne avevamo bisogno”, conclude Alexis Ducancel.
Circa cinquanta dipendenti lavorano oggi nel sito di produzione Genzyme, dove sono eseguiti lotti di produzione iniziali per validare il processo di produzione. La piena produzione dovrebbe iniziare alla fine del 2011, quando saranno state ottenute le certificazioni AFSSAPS. Il numero totale di dipendenti dovrebbe quindi salire a 270.
Didascalia 1:
Il nuovo sito Genzyme per la produzione di anticorpi policlonali per trapianti ed ematologia copre 22.000 m². Esso ha richiesto un investimento di 115 milioni di euro.
Didascalia 2:
La gamma Anybus Communicator permette di ritrasmettere dati seriali a un sistema di controllo centrale.
Note su Genzyme
Genzyme è stata costituita a Cambridge, Massachusetts (Stati Uniti) nel 1981, quando i suoi fondatori hanno accettato la sfida di fornire soluzioni per pazienti affetti da malattie serie per le quali, all’epoca, non esisteva cura. Un approccio personalizzato alla salute, unito all’impegno ad innovare, la rendono un’azienda di biotecnologia avanzata, riconosciuta in tutto il mondo. Benché aiutare pazienti affetti da malattie genetiche rare rimanga la sua missione primaria, Genzyme offre anche trattamenti innovativi per aiutare pazienti con malattie renali, cancro e artrite o che richiedono un trapianto o un intervento chirurgico, oltre a lavorare in campi come gli esami diagnostici. Genzyme, un’azienda pioniera nella biotecnologia, è oggi una società internazionale diversificata, che impiega 11.000 dipendenti in tutto il mondo.
“Nel sito Sanofi Pasteur di Marcy, Genzyme sta attualmente utilizzando metodi di produzione a elevato contenuto di manodopera. Con questo nuovo sito, ci auguriamo di ottimizzare il processo in modo da ridurre l’errore umano al minimo assoluto. Questo processo a lotti altamente sequenziale implica oltre 780 fasi di produzione. Vi sono quindi numerose sorgenti di errore. Automatizzare un processo come questo ha richiesto molto stretto lavoro con le apparecchiature coinvolte per decidere come il sistema doveva comportarsi. Ciò ha evitato la necessità di ripensare l’intera ergonomia dell’edificio e delle apparecchiature di produzione, pur traducendosi in una vera rivoluzione nel modo in cui il processo di produzione funziona. Per ottenere tale risultato, abbiamo specificato oltre 4.000 parametri e 13.000 allarmi, che ci hanno permesso di governate ogni fase della produzione”, spiega Alexis Ducancel, responsabile Sistemi Automatizzati di Genzyme.
Bioproduzione: una serie di processi complessi
A differenza della chimica tradizionale, la produzione basata su cellule vive implica molte fasi differenti complesse e costose. Il ciclo di produzione di una proteina ricombinante richiede un’infrastruttura industriale adatta per la produzione a larga scala, che implica numerose fasi scaglionate su diversi mesi. Ogni fase è soggetta a numerosi controlli di qualità. Durante l’intero ciclo di produzione vengono effettuati test per assicurare l’assenza di virus e contaminanti. Alla fine della linea, si controllano anche la purezza e l’azione della proteina.
La produzione di questo farmaco implica molte fasi complesse, punteggiate da una successione di test tecnici e di verifica della qualità. Il processo di produzione può essere suddiviso in quattro fasi principali:
- La raccolta delle immunoglobuline, che avviene iniettando tessuto umano in conigli.
- La purificazione delle immunoglobuline per rimuovere proteine indesiderate (soprattutto anticorpi antieritrociti), tramite emoassorbimento.
- La fase di cromatografia consiste nello scambio anionico tramite l’uso di una resina di scambio ionico. Le impurità sono catturate dalla resina, mentre le immunoglobuline, che non hanno carica negativa, sono eluite. Questa fase è verificata mediante spettrofotometria ed elettroforesi.
- La fase di precipitazione serve per eliminare le ultime impurità rimanenti. Le immunoglobuline purificate sono pastorizzate (a 60°C per 10 ore).Questa soluzione è essiccata tramite raffreddamento prima di essere sigillata in fiale.
“In questo processo possiamo, ad esempio, programmare le impostazioni delle centrifughe (velocità, temperatura, tempo di funzionamento, ecc.). Questi valori possono essere modificati nello SCADA per tenere conto delle specifiche esigenze dell’attuale lotto di produzione. Le letture vengono effettuate in ogni fase e ritrasmesse allo SCADA. Questo ci permette di mettere in atto un processo di tracciabilità molto preciso. In particolare, ciò significa che il carico di lavoro per i team di verifica della qualità è significativamente ridotto, con un conseguente vantaggio in termini di costi”, aggiunge Alexis Ducancel.
Il sito di Lione, come quello di Marcy, riceverà le omologazioni FDA e AFFAPS.
“Naturalmente, abbiamo scelto HMS perché sentivamo che nessun’altra azienda aveva soluzioni standard a disposizione per restituire dati da un set di apparecchiature molto eterogenee, che non sono state necessariamente progettate per il collegamento a fieldbus. Abbiamo 28 centrifughe, pH-metri, bilance e così via. I protocolli d’interfaccia variano: seriale o ASCII, per esempio. I 30 Anybus Communicator sul posto ritrasmettono i dati su Ethernet o Profibus allo SCADA centrale”.
Anybus Communicator: la soluzione per integrare apparecchiature seriali in una rete di comunicazione industriale
La serie di gateway Anybus Communicator per il collegamento a Ethernet industriale/Fieldbus permette di collegare in rete dispositivi che sono stati sviluppati per l’uso in una rete seriale. L’Anybus Communicator può collegare la maggior parte dei prodotti con interfaccia seriale RS-232/422/485 a un’Ethernet industriale o un fieldbus. Esso esegue una conversione intelligente fra il protocollo seriale e la rete di destinazione. Tale conversione è configurata usando il software “ABC Config Tool”. La configurazione di rete, una volta completata, può essere riutilizzata per tutte le reti supportate dal Communicator.
“A parte la qualità del prodotto, abbiamo scoperto che il supporto tecnico era presente ogni volta che ne avevamo bisogno”, conclude Alexis Ducancel.
Circa cinquanta dipendenti lavorano oggi nel sito di produzione Genzyme, dove sono eseguiti lotti di produzione iniziali per validare il processo di produzione. La piena produzione dovrebbe iniziare alla fine del 2011, quando saranno state ottenute le certificazioni AFSSAPS. Il numero totale di dipendenti dovrebbe quindi salire a 270.
Didascalia 1:
Il nuovo sito Genzyme per la produzione di anticorpi policlonali per trapianti ed ematologia copre 22.000 m². Esso ha richiesto un investimento di 115 milioni di euro.
Didascalia 2:
La gamma Anybus Communicator permette di ritrasmettere dati seriali a un sistema di controllo centrale.
Note su Genzyme
Genzyme è stata costituita a Cambridge, Massachusetts (Stati Uniti) nel 1981, quando i suoi fondatori hanno accettato la sfida di fornire soluzioni per pazienti affetti da malattie serie per le quali, all’epoca, non esisteva cura. Un approccio personalizzato alla salute, unito all’impegno ad innovare, la rendono un’azienda di biotecnologia avanzata, riconosciuta in tutto il mondo. Benché aiutare pazienti affetti da malattie genetiche rare rimanga la sua missione primaria, Genzyme offre anche trattamenti innovativi per aiutare pazienti con malattie renali, cancro e artrite o che richiedono un trapianto o un intervento chirurgico, oltre a lavorare in campi come gli esami diagnostici. Genzyme, un’azienda pioniera nella biotecnologia, è oggi una società internazionale diversificata, che impiega 11.000 dipendenti in tutto il mondo.
Richiedi maggiori informazioni…